کوره
کوره وسیله یا محلی است که در آن حرارت ایجاد میکنند. در زبان فارسی به آن آتشدان و آتشگاه نیز گفته میشود.[1] همچنین سیستم حرارت مرکزی ساختمانها بهطور معمول بر پایه یک کوره بنا شده که در آن یک سیال در دیگهای پرهدار گرم میشود.[2] واژه کوره همچنین به اختصار به کورههای صنعتی تولید حرارت در پالایشگاهها، برجهای تقطیر، آهنگریها، استخراج فلزات، کارخانجات سرامیکسازی و واحدهای شیمیایی بهکار میرود. انرژی موردنیاز کوره گاهی بهطور مستقیم از سوزاندن سوخت تأمین میشود. در برخی از کورهها نیز انرژی مورد نیاز برای تولید گرما با استفاده از انرژی الکتریکی، خواه به روش قوس الکتریکی و خواه به روش القای الکترومغناطیسی تأمین میشود.[3]
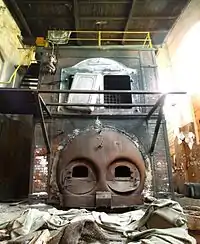
کورههای مصالح ساختمانی
کورههای مصالح ساختمانی، کورههایی هستند که به منظور ساخت مصالح از آن استفاده میشود.
کورههای گچ پزی
سنگ گچ را بیشتر در ۳ نوع کوره میپزند:
۱.کوره تنورهای باستانی ایرانی: سنگ گچ را در آن میچینند و تون کوره را آتش میکنند تا سنگ گچ بپزد. چنین گچی دارای جنس همگن نیست، زیرا نزدیک به ۲۰٪ آن گچ پخته ساختمانی با نیم مولکول آب و ماندهٔ آن یا سوخته یا نپخته است.
در ایران، روی کورههای تنوره ای آهک پزی و آجرپزی سنگ گچ میگذارند تا در گرمای کم بپزد و آن بهترین گچ برای سفیدکاری است.
۲.کورههای تاوهای: سنگ گچ را در سنگشکن کلوخه کرده، آسیاب میکنند تا گرد شود. به گرد سنگ گچ در تاوههای بزرگ گرما میدهند (مانند بو دادن آرد) تا بپزد. گرد سنگ گچ درون تاوه را پیوسته هم میزنند تا همهٔ گرد سنگ یکنواخت بپزد.
این روش گچ پزی با کار ناپیوسته است.
۳.کورهٔ گردنده: کار کوره گردنده گچ پزی پیوسته است. برای پختن گچ در آن، سنگ گچ را کلوخه میکنند و آن را در کوره گرداننده میریزند. به پوستهٔ فولادی کورهٔ گردنده گرما میدهند و از لولهٔ درون کورهٔ گردنده هم گاز گرم می گذارند و بخار برخاسته از سنگ را به بیرون میمکند. این بخار آب هنگام بیرون رفتن از کوره، نزدیک به ۱۰۰ تا ۱۲۰ درجه گرما دارد. کلوخهٔ سنگ گچ پخته در کورهٔ گردنده را به نرمی خواسته شده آسیاب میکنند.
کوره آجر پزی
پس از خشک شدن خشت، آن را در کوره میچینند به طوری که به همدیگر نچسبند، تا هوا، شعله و گاز از لای آجرها بگذرند. کورههای آجرپزی سه نوع اند: کورهٔ با آتش ثابت و آجر ثابت، کورهٔ با آتش رونده و آجر ثابت و کورهٔ با آجر رونده و آتش ثابت.[4]
کورهٔ با آتش ثابت و آجر ثابت یا کورهٔ تنورهای: این کورهٔ کارش پیوسته نیست. کورهٔ تنورهٔ کوتاه و گشادی است که خشت را در آن میچینند و تون آن را میتابند (آتش میکنند) شعله، هوای داغ و دود از لابه لای خشتهای چیده شده در کوره بالا میروند و گرمای خود را به خشتها پس میدهند و خشتها میپزند.
کار کوره تنورهای پیوسته نیست و در آن گرمای زیاد به هدر میرود زیرا پس آنکه خشت پخت و آجر شد، سر کوره را باز میکنند و میگذارند آجر درون کوره سرد شود و گرمایش را به هوا بدهد.
جنس آجری که در کورهٔ تنورهای پخته شود یک جور نیست. از پایین به بالا جوش، آجر جوش، آجر سبز، آجر بهی، آجر سفید، آجر ابلق، آجر قرمز و آجر نیم پخته به دست میآید.
اگر بالای کورههای تنوری به شکل قارچ نیز ساخته شد و سر کوره نیز پوشیده شود، به طوری که که گاز کوره از بالای آن بیرون نرفته، از سوراخهای نزدیک کف کوره به دودکش یا هوا کش مکیده شود. گاز داغ، گرمایش را به خشتهای چیده شده در کوره پس میدهد. با این کار، گرمای گاز کوره هدر نمیرود و جنس آجرها هم همجور میشود.
کوره با آتش رونده و آجر ثابت: کار این کوره پیوسته است و گرمای آن خیلی کم هدر میرود. این کوره را نخست یک بنای اهل برلن به نام friedrich hoffmann ساخت که به نام او مرسوم است. چون حلقهای ساخته میشد، آن را کوره حلقهای هوفمان نامیدند.
نخستین کورهها به شکل دایرهای ساخته میشدند. اکنون آن را به شکل حلقهای دراز یا آرهای و مانند اینها میسازند. در این کورهها از هدر رفتن گرما به اندازهٔ زیاد جلوگیری میشود.
کورهٔ تونلی: در آن سفالهای ممتاز هم میپزند. کارش مانند تونل خشت خشک کنی است. از سر تونل واگونک با بار خشت به تونل میرود و از ته تونل، آجر سرد شده بیرون میآید. کانون آتش در دیوار درونی تونل جا دارد. همین که واگونک با بار خشت به درون تونل رانده شد، به کندی به سوی کانون آتش پیش میرود. خشت کمکم گرم و نیمه پز شده، از برابر کانون آتش گذشته میپزد. هنگامی که واگنک آجر پخته به سوی ته تونل میرود، به آن هوای سرد میدمند تا گرمای آجر را بگیرد و آن را سرد کند. هوایی که از روی آجر میگذرد، داغ میشود و هواکش پهلوی کانون آتش آن را مکیده به کانون آتش میدمد.
کار کورهٔ تونلی پیوسته است و گرمای آن خیلی کم هدر میرود، اما ساختن تونل ریل گذاری، ارزش واگنکها و جز اینها گران است. جایی که برق ارزان باشد، میشود کوره تونلی را برقی ساخت و کوره را با برق روشن کرد.
برای آنکه کوره تونلی دراز نشود، آن را در ۲ تکهٔ پهلوی هم میسازند. در یک تکه خشت میسازند و روی واگنک میچینند و به گرم خانه میبرند تا در آنجا خشتهای روی واگنکها خشک، گرم و داغ شوند، سپس واگنکهای با بار خشت داغ را به درون تکه دوم میرانند در تکه دوم که کوره در آن ساخته شده، خشتهای داغ شده از برابر کانون آتش گذشته، میپزند. روی آجر داغ هوا میدمند و گرمای آن را میگیرند. هوای داغ شده را به گرم خانه و به کانون آتش میدمند.
کوره شیشهگدازی
مواد خام شیشه را در کورههای شعلهای (که خمیر شیشه با سوخت برخورد ندارد) آب میکنند. برای مقداری کم، تغارهای نسوز به گنجایش چند تن و برای مقدار زیاد کوره تشتی با تاق گنبدی به گنجایش تا ۱۲۵۰ تن ساختهاند. بیشتر کورههای شیشه گدازی کفشان ۲۵۰ متر مربع است که روی آن تا بلندی یک متر شیشه خمیر شده میایستد. گرمای شعله ۱۵۰۰ تا ۱۶۰۰ درجهی سانتیگراد است و در گرمای ۱۴۵۰ درجه شیشه خمیر شل همگن میشود. درون کوره با آجر نسوز پوشیده شده، تا شیشه گداخته و گرمای کوره در آن اثر نکند.
کورهٔ اجاقی زیمنس مارتین
آن را زیمنس آلمانی و برادران مارتین بلژیکی همزمان در سال ۱۸۶۴میلادی ساختند. کوره زیمنس مارتن از تانک مخلوط کن گهوارهای بارگیری میشود و فولاد قراضه و دم قیچی کارخانه فولادسازی هم به آن میافزایند. جنس آستر کوره بستگی به آهن خامی دارد که در آن عمل آورده میشود. اگر فسفر آهن خام زیاد باشد، کوره با آجر نسوز بازی و هرگاه فسفرش کم باشد، با آجر نسوز اسیدی آستر میشود. بیشتر آجر نسوز منیزیتی یا دولومیتی مصرف می گردد.[5]
در کورهٔ فولادسازی زیمنس مارتن، سرباره هم درست میشود هرگاه آهن خام فسفر دار در آن ریخته شده باشد، سرباره آن فسفات کلسیم میگردد، که با آن کود میسازند و چنانچه آهن خام کم فسفر در آن ریخته باشند سرباره آن را به کوره آهن گدازی میریزند.
برای سوزاندن کربن و آبکی نگاه داشتن آهن خام، به آن شعله میدمند. با دمیدن گاز داغ و هوای داغ به کوره، شعله روی آهن خام زبانه میکشد و کربن آن را میسوزاند، بیآنکه نیاز به هم زدن آهن خام درون کوره باشد. از این رو فولادسازی در کورهٔ زیمنس مارتن کند پیش میرود و هر پخت تا ۹ ساعت به درازا میکشد، اما جنس فولادش ممتاز و ناخالصی آن کم است، زیرا در برابر شعله عمل میآید. این کوره با گنجایش از ۵ تا ۳۰۰ تن ساخته شدهاست.
پیش از دمیدن گاز سوخت و هوا به کوره، آنها را از درون داغ کنها میگذرانند تا داغ شود. برای داغ کردن داغ کنها، از گرمای گاز سوخته کوره بهرهگیری میشود.
پیش از آنکه گاز سوخته کوره به دودکش برود آن را از توی داغ کنها میگذرانند تا گرمایش را پس بدهد، سرد شود و به دودکش برود. در کورهٔ زیمنس مارتن هم همه کربن آهن خام را میسوزانند و از نو به آن کربن میزنند. پیش از خالی کردن کوره، عنصرهایی را که باید با آهن هم جوش شوند تا فولاد خواسته شده ساخته شود، به حال چند جوش به کوره مکی ریزند. پس از آنکه فولاد عمل آمد، با سیخ زیر آب کوره را میزنند تا فولاد درون آن (که نزدیک به ۹۰ تن است) به بیرون روان گردد.
فولاد آبکی ای در پاتیل بسمر یا پاتیل توماس یا کورهٔ زیمنسن مارتن ساخته شود، در فولاد ریزی مصرف میگردد، یا آنکه فولاد آبکی را در تنورهای چدنی میریزند تا به شکل شمش در آید، شمش فولاد سرخ شده را از تنور بیرون میآورند و زیر پتکهای سنگین میکوبند، همین که به شکل شمش دراز درآمد تکهتکه میبرند. تکههای فولاد را از نو در کوره میگذارند تا سرخ شوند و به آنها شکل میدهند.[6]
کوره چدن
چدن، کربور آهن است که از آهن خام ساخته میشود و خیلی کم از کوره آهن گدازی بیرون میآید. برای ساختن چدن، آهن خام را در کوره کوپل یا کورهٔ شعلهای، یا کورهٔ برقی، از نو آب کرده، کربن، فسفر، منگنز، سیلیسم و عنصرهای دیگر را در آن میاندازند، کمی هم آهن قراضه به آن میافزایند. در کورهٔ، ناخالصیها به شکل سرباره رو میآیند که آن را میگیرند تا چدن خواسته شده به دست آید.
۱.کوره کوپل: همانند کورهٔ آهنگدازی بلند، کوچکتر است با بهرهدهی ۴ تا ۹ تن در ساعت. این کوره به شکل استوانهای است که درون آن با آجر نسوز آستر شدهاست آهن خام و کک را لایه به لایه به کوره میریزند و اگر نیاز باشد، گدازآور هم به آن میافزایند (با گدازآور آهکی، سرباره را آبکی میکنند) و گرمای کوره را بالا میبرند در این کوره برای ساختن هر تن چدن، به ۱۰۰ تا ۱۵۰ کیلوگرم کک نیاز است. از آهن خام در موره کوپل با ۳ تا ۶ درصد افت چدن میسازند. همچنین با از نو آب کردن آهن خام در کوره کوپل و ساختن چدن از آن، کربن، سیلیسیوم و گوگرد آن هم کاهش مییابد.
۲. کوره شعلهای: تشت بزرگ سرپوشیدهای است که در آن آهن خام میریزند و رویش شعله میدمند تا کربن زیادی آن بسوزد و چدن شود. مصرف سوخت در کوره شعلهای زیاد است و نیاز به گدازآور ندارد. در کورهٔ شعلهای، با سوختن کربن و دیگر عناصر آهن خلم، ۶ ال ۱۰٪ از وزن آن کم میشود تا چدن خواسته شده ساخته شود.
۳. کوره برقی: در کورهٔ چدنهای ویژه و چدنهای با تاب زیاد ساخته میشود. برتری کوره برقی به دو کورهٔ دیگر آن است که میتوان درجهٔ گرمای کوره را بالا برد و آن را ثابت نگاه داشت در کوره برقی سرباره درست نمیشود. اگر سیلیسیوم در چدن زیاد باشد، کربن آن به شکل برگ گرافیت جدا میشود. فسفر، چدن را ترد و آبکی میکند، میتوان با آن چیزهای ظریف ریخت. گوگرد، چدن را کند روان میکند. منگنز چدن را سخت میسازد.
کورهٔ آهنگدازی
دارای تنوره، آتش خانه و بوته است. تنوره در بالا، آتشخانه در میانه و بوته در پایین کوره جا دارند. پوستهٔ بیرونی کورهٔ آهنگدازی بلند را بتنی یا فولادی میسازند و بوتهٔ درونی آن را با آجر نسوز میپوشانند. بالای تنوره در پوشی است که از بیرون رفتن گاز کوره جلوگیری میکند. دوره در پوش کورهٔ بلند، ایوانی است که کوره از آنجا بارگیری میشود. با مخلوط کلوخه سنگ اکسید آهن و سنگ گدازآور و سوخت کوره را بارگیری میکنند.
سوخت را در یک لایه و مخلوط کلوخهٔ سنگ آهن و گدازآور را در لایهٔ دیگر پی در پی از ایوان بالای تنوره به کوره میریزند. بار کوره به آهستگی به سوی پایین کوره سر میخورد. در آغاز خشک شده، سپس از سنگ آهک co2 و از سنگ آهن جدا گشته و در پایین تنوره و در آتش خانه ترکیبهایی نو پیدا میشوند.
آهن کربن میگیرد آهن خام میشود و به دون میچکد، آهک و سیلیس سنگ آهن هم تفاله درست میکنند که جنسش سیلیکات کلسیم است و به درون بوته میچکد. چون آهن خام از تفاله سنگین تر است در پایین بوته روان میشود و تفاله که سبکتر است روی آن جا میگیرد. آهن خام را در هر ۴ تا ۶ ساعت و تفاله را پیوسته از بوته به بیرون روان میسازند.
کورههای سیمانپزی
۱. رایجترین و متداولترین کورههای سیمان پزی کورههای سیمان پزی کورهٔ گردندهٔ خفته است که عبارت است از یک استوانهٔ فلزی به طول تقریبی ۱۰۰ متر و به قطر تقریبی ۴ متر که ضخامت بدنه آن ۲۰ تا ۴۰ میلیمتر است در حدود ۳ تا ۴٪ نسبت به افق شیب دارد و ۵/۱ تا ۲ دور در دقیقه حول محور خود میچرخد. این لوله بلند روی پایههایی قرار دارد یک موتور با چرخ دنده حرکت دورانی آن را تامین میکند. کار این نوع کورهها پیوسته است.
۲. دیگر از انواع کوره سیمان پزی کوره ایستاده میباشد این کوره استوانهای است به قطر حدود ۳ متر که دهانه بالای آن گشادتر است طول این نوع استوانه ۱۰ متر است خوراک کوره را با رطوبت به صورت گلولههایی به قطر تقریبی ۱۰ سانتیمتر درمیآورند و آن را از بالا با زغال کک به کوره میریزند و کوره را از پایین آتش میکنند و پس از پختن، کلینکر را از زیر کوره خارج مینمایند از این نوع کورهها تا ظرفیت روزانه ۳۰۰ تن هم ساخته شدهاست.[7]
منابع
- دهخدا، علیاکبر. «کوره». دریافتشده در ۲۱ آذر ۱۳۹۰.
- «گرمایش مرکزی». سازمان بهینهسازی مصرف سوخت. بایگانیشده از اصلی در ۱۱ دسامبر ۲۰۱۱. دریافتشده در ۲۱ آذر ۱۳۹۰.
- Johnson, Bill; Standiford, Kevin (2008-08-28). «Practical Heating Technology».
- Ahmed, Rifat (2020-06-01). «Handbook on Single, Multi & Variable Speed Furnaces» (PDF).
- مصالح ساختمانی-تالیف:احمد حامی
- «Furnace». HVAC, Air Conditioning & Furnace, Repair & Installation in GTA (به انگلیسی). دریافتشده در ۲۰۲۱-۰۲-۲۱.
- مصالح شناسی-تالیف:سیاوش کباری
![]() |
در ویکیانبار پروندههایی دربارهٔ کوره موجود است. |