ریختهگری لاست فوم
ریختهگری به روش لاست فوم (به انگلیسی: Lost-foam casting) روشی جدید در تولید قطعات ریخته است که از سال ۱۹۶۰ در حال گسترش است. اگرچه استفاده از این روش در دیگر بخشهای ریختهگری به عنوان یک فناوری کامل به یک رؤیا شبیه است اما از این روش در ریختهگری آلومینیومی، چدن خاکستری و داکتیل استفاده میشود.
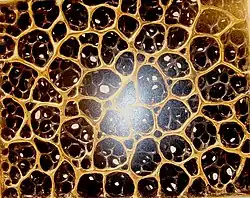
روش ریختهگری با مدل فومی فداشونده، گونهای از فرآیندهای ریختهگری با مدل تبخیر شونده است. این روش بسیار شبیه به روش ریختهگری دقیق است، با این تفاوت که در آن به جای موم از فوم استفاده میشود. برتری اصلی این روش نسبت به ریختهگری دقیق (با موم) حذف مرحله ذوب و خارج کردن موم از قالب است. این کار با بهرهگیری از دمای ذوب و چگالی بسیار پایین فوم میسر میشود.
تاریخچه
روش ریختهگری با فوم فداشونده در اوایل دهه پنجاه میلادی توسط مجسمهساز کانادایی، آرماند ویلنکورت (به انگلیسی: Armand Vaillancourt) اختراع شدهاست. مزایای این روش در اواسط دهه ۱۹۸۰ میلادی توسط جنرال موتورز به عموم شناسانده شد؛ هنگامیکه اعلام شد از این روش در خط تولید خودروی جدید آن، ساترن، استفاده خواهد شد. نخستینبار جنرال موتورز از این روش برای تولید تمام بلوک سیلندرها، سرسیلندرها، میل لنگها، دیفرانسیلها و جعبههای انتقال قدرت استفاده میکردهاست.
فرایند ریختهگری لاست فوم
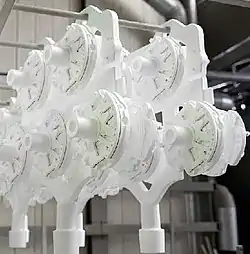
در ریختهگری به روش لاست فوم، از مدلهایی که از پلی استایرن منبسط شده (فوم) ساخته شده استفاده میگردد و در درون ماسه بدون چسب قرار داده میشود. از مزایای استفاده از مدل فومی این است که هم مراحل ریختهگری و هم قطعه ریخته را با حذف ماهیچه بهبود میسازد و همچنین میزان دقت را بالا میبرد. چون فضای داخلی مدل فومی توسط ماسه بدون چسب پر میگردد ومدل فومی حفرههای داخلی قطعه را خود ایجاد میکند نیازی به ماهیچه نیست.
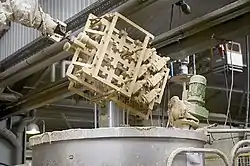
با حذف ماهیچه میتوان از مدل فومی برای قالبگیری قطعاتی که شکل هندسی پیچیده و مشکلی دارند استفاده کرد. برخلاف سایر روشهای ریختهگری نیازی نیست که مدل از قالبگیری اولیه به «casting» بازگردانده شود. به مدل فومی باید روکشی از سرامیک داده شود. جنس مدلهای فومی از پلی استایرین منبسط شده یا «PMMA» است که با ریختن مواد مذاب به درون قالب فومی تبخیر میشود.
استفاده از دانههای کمتراکم و از پیش-منبسط شده (Pre-expanded) در تهیه مدل فومی، باعث کاهش گاز متصاعد شده ناشی از تبخیر فوم میگردد. ممکن است که یک مدل از چندین قسمت یا چندین مدل که در یک خوشه با هم ترکیب شده و به هم چسبانده شدهاند تشکیل یابد. هنگامیکه مدل ساخته شد باید روکشی از سرامیک یا سایر مواد نسوز به مدل داده شود که این عمل را از طریق فروبردن مدل در داخل رنگ (روکش سرامیکی) یا از طریق پاشیدن صورت میپذیرد. همانند سایر روشهای ریختهگری این روش نیز سیستمهای «gating» و «risering» را دارا میباشد. با این تفاوت که سیستمهای «gating» و «risering» به مدل چسبانده میشوند. نمونه در داخل درجه آویزان میشود و ماسه بدون چسب به داخل درجه در حالیکه درجه در حال ویبره است ریخته میشود که این ویبره برای این است که ماسه کاملاً مدل را احاطه کند.
به هنگام ریختن مواد مذاب فوم تبخیر میشود و از درجه خارج میگردد. استحکام ماسه و وجود روکش روی فوم باعث میشود که قالب در همان حالت خود باقی بماند. بعد از اینکه مواد مذاب سرد و جامد شد به واحد «shakeout» ارسال میگردد و سایر مراحل همانند سایر روشهای ریختهگری به ترتیب صورت میپذیرد. در این روش چون از ماسه بدون چسب استفاده میشود پروسه «shakeout» به واسطه وجود آن تسهیل یافتهاست.
مشخصات و محدودیتهای ابعادی روش
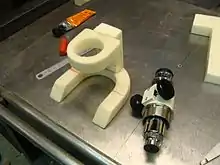
فلزهای متداولی که به وسیله این روش ساخته میشوند شامل چدنها، آلیاژهای آلومینوم، فولادها و آلیاژهای نیکل هستند. از موارد کم مصرف تر میتوان به فولادهای زنگ نزن و آلیاژهای مس نیز اشاره کرد. بازه اندازهای که این روش پوشش میدهد از ۰٫۵ کیلوگرم شروع شده و تا چندین تن ادامه پیدا میکند. حداقل ضخامتی که این روش پوشش میدهد ۲٫۵ میلیمتر بوده و حد بالایی برای آن وجود ندارد. صافی سطح متداول برای این روش از ۲٫۵ تا ۲۵ میکرون میباشد. تلرانس خطی متداول آن نیز ±0.005 mm/mm است.
اجزای فرایند
مدل فومی
مدلهای فومی این فرایند از پلی استایرن منبسط شده (EPS) که مادهای ترموپلاستیک و شامل ۹۲ در صد کربن و ۸ در صد هیدروژن است ساخته میشوند. این ماده شامل یک عامل فرّار و پفکننده هیدروکربنی ست که باعث میشود ذرات پلی استیرن تا چگالی ۱۸ کیلوگرم بر مترمکعب منبسط شوند و با چگالی کم بتوانند علاوه بر حفظ صلبیت، قالبهای پیچیده را پر کنند.
انبساط ذرات متراکم EPS طی دو مرحله انبساط اولیه و قالبگیری انجام میشود.
در مرحله اول، دانههای EPS حرارت داده شده و منبسط میشوند تا به چگالی مورد نظر برای مدل نهایی برسند. در مرحله بعد دانههای منبسط شده وارد قالب نهایی شده و بر اساس حرارت بزرگتر شده و فضای خالی بین خود و همچنین گوشهها را پر میکنند.
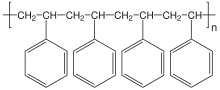
حرارت دهی مرحله ثانویه توسط بخار آب انجام میشود. بخار آب از یک سمت وارد قالب شده و از سمت دیگر خارج میشود. سپس همین عمل در جهت معکوس انجام میشود تا نهایتاً دانهها تمام محفظه داخل قالب را پر کنند. خنک کاری مدلها توسط پاشش آب به دیواره قالب یا ایجاد خلأ اتفاق میافتد تا فشار داخل هر ذره کم شده، دیواره آن سخت شود و پس از خروج از قالب شکل آن حفظ گردد.
اندازه دانههایی که انبساط اولیه را گذراندهاند لازم است به حدی باشد که در باریکترین مقاطع مدل، حداقل سه دانه در کنار هم قرار گیرند. این مدلها به مرور زمان منقبض میشوند که لازم است حین طراحی، این انقباض علاوه بر انقباض ناشی از انجماد در نظر گرفته شود. انقباض مدل به عوامل متفاوتی از جمله ابعاد و چگالی دانتههای EPD، عمر دانهها قبل از انبساط اولیه و قالبگیری بستگی دارد. بیشتر انقباض در ۳۰ روز اول بعد از تولید مدل اتفاق افتاده و میزان آن میتواند تا حدود ۰٫۸ درصد باشد.
بسته به نوع پلیمر مورد استفاده، نوع ماده منبسط کننده، دمای بخار آب و زمان بخاردهی، زمان خارج کردن مدل از قالب، دقت ابعادی مدل فومی متغیر خواهد بود. مدلهای فومی دارای چگالی مختلف، مقدار گاز متفاوتی در حین تجزیه تولید میکنند. هرچه چگالی مدل فومی بیشتر باشد، مقدار گاز تولیدی نیز بیشتر خواهد بود. مقدار گاز تولید شده بر سرعت حرکت مذاب درون قالب تأثیر دارد.
پوشان
مدل فومی قبل از قالبگیری توسط دوغابی پوشش داده میشود که این دوغاب پس از خشک شدن پوستههای محکمی بر روی سطح مدل ایجاد میکند. پوشش دهی مدل به دو صورت غرق در حوضچه یا اسپری شدن مواد پوشان انجام میشود.
ترکیب شیمیایی پوشان شامل پودر ماده دیرگداز، ماده معلق کننده، چسب، مواد دگرروانی و حامل تشکیل شدهاست. پودر دیرگداز معمولاً از سیلیس، آلومینا، زیرکن، کرومیت و آلومینوسیلیکاتهایی نظیر مولایت و پیروفیلایت تشکیل میشود. پوشان در چندین مرحله بر روی مدل اعمال و فرایند خشک کردن معمولاً در دمای ۵۰ تا ۶۰ درجه سانتی گراد و در زمان ۲۴ ساعت در خشک کن انجام میشود. ضخامت پوشان معمولن حدود ۰٫۲۵ تا ۰٫۵ میلیمتر است.
از مهمترین ویژگیهای پوشان میتوان به قابلیت نفوذپذیری آن اشاره کرد. هرچه ضخامت پوشان بیشتر باشد، قابلیت نفوذپذیری آن کمتر است. بسته به دمای ذوب فلز، مواد حاصل از تجزیه فوم ممکن است به صورت گاز یا مایع باشند. برای مثال این مواد در چدن به صورت گازی و در آلیاژهای آلومینوم به صورت مایع میباشند. مدل فومی به دلیل تشعشات ناشی از مذاب، در جلوی آن ذوب میشود و لازم است در زمان مناسبی از طریق منافذ پوشان به درون ماسه نفوذ کنند.
مهمترین هدف استفاده از پوشان، نگه داشتن ماسه و جلوگیری از فروریختن آن است. اعمال پوشان همچنین حرارت را درون مذاب حفظ کرده و سیالیت آن را افزایش میدهد. به دلیل جلوگیری از تغییر شکل مدل فومی در حین قالبگیری و ارتعاش، دقت ابعادی را حفظ میکند.
قالبگیری
درجه در سه مرحله با ماسه خشک روان حاوی کربن پر میشود و پس از هر مرحله، در سه جهت ویبره شده تا تمامی حفرات قطعه را پر کند. هنگام تزریق ماسه یک صفحه فلزی کوچک بالای قطعه قرار میگیرد تا از آسیب احتمالی به مدل فومی جلوگیری شود.
درجه از کف، تحت مکش هوا قرار میگیرد تا ماسه تا حد امکان متراکم و مستحکم شود. کف درجه نیز با فیلترهایی پوشانده میشود تا از خروج ماسه جلوگیری به عمل آید.
مزایا و معایب
مزایا
این فرایند برای ریختهگریهای بسیار پیچیده که معمولاً به ماهیچه نیازمندند بسیار سودمند است. این روش همچنین از لحاظ ابعادی بسیار دقیق است، به دلیل پایین آوردن سرعت سرد شدن، تاب برداشتن و ترکهای سطحی نیز کم میشود، صافی سطحی عالی را حفظ میکند و قابلیت تولید قطعات با شیب منفی را دارا میباشد.
ساخت قطعات پیچیده که به صورت یک تکه قابل ساخت نیستند به وسیله این روش امکانپذیر میشود؛ به این دلیل که میتوان قسمتهای مختلف یک شکل و راه گاههای آن را به صورت جدا ساخته و سپس به وسیله چسب آنها را سرهم کرد.
دیگر مزایای این روش شامل حذف سطح جدایش، کاهش اتلاف مواد اولیه و سریع و ارزان بودن مدل فومی است. برای ساخت قطعات با تعداد بالا، میتوان آنها را به صورت خوشههایی سرهمبندی کرد که این کار به کم شدن مراحل پوشش دهی و قالبگیری و افزایش بازده میانجامد.
یکی از مزایای اصلی این روش استفاده از ماسه بدون چسب است. این ماسه به راحتی قابل بازیافت بوده، از کانالهای قطعه به راحتی خارج شده و میزان آلودگی محیط زیست را نیز کاهش میدهد.
این روش به دلیل داشتن مراحل کمتر نسبت به ریختهگری دقیق، از لحاظ اقتصادی به صرفه تر است.
معایب
اولین عیب این روش از بین رفتن مدل در هر بار قالبگیری ست. به همین دلیل ممکن است روش برای حجم تولید پایین به صرفه نباشد. همچنین مدلهای فومی ساخته شده، به دلیل استحکام پایین فوم، ممکن است شکننده و آسیبپذیر باشند و دقت زیادی در جابجایی و نگهداری آنها لازم است. همچنین اگر برای ساخت مدلها از قالب استفاده شود، هزینه اولیه بالا خواهد بود.
جستارهای وابسته
منابع
مشارکتکنندگان ویکیپدیا. «Lost-foam casting». در دانشنامهٔ ویکیپدیای انگلیسی، بازبینیشده در ۲ اکتبر ۲۰۱۱.
https://en.wikipedia.org/wiki/Lost-foam_casting
بررسی اثر دانسیته فوم و ضخامت پوشان بر الگوی جریان و برخی پارامترها در ریختهگری فومی/محمد خدائی و ناصر ورهرام
https://web.archive.org/web/20120726054306/http://nmpa.ir/files/157.doc