شکلدهی چرخشی
شکل دهی چرخشی فلز (به انگلیسی: Metal spinning) یکی از روشهای شکلدهی فلزات است که در آن از ترکیب نیرو و چرخش، جهت ایجاد اشکال تو خالی با محور تقارن و بدون درز استفاده میشود.[1]
اساس فرایند شکلدهی چرخشی، را میتوان مشابه عملکرد چرخ سفالگری دانست که با چرخش قطعه و اعمال نیروی نقطهای انجام میشود. در این روش مواد اولیه که عمدتاً به شکل ورق (یا لوله در فلو فرمینگ) میباشند بین مندرل (mandrel) و ابزار شکل دهی، تحت فشار قرار گرفته و شکل میگیرد. این فرایند یکی از اقتصادیترین روشها در تولید محدود و نمونه سازی برای ساخت قطعات فلزی با تقارن محوری میباشد.
با این روش قطعاتی با اشکال مخروط، نیم کره، لوله، استوانه، یا ترکیبی از اینها که توخالی هستند، در تنوع گستردهای از جهت اندازه و کانتور ساخته میشود. اگرچه ساخت قطعاتی با اشکال بیضوی هم با این فرایند امکانپذیر است ولی به آسانی شکلدهی قطعات استوانهای نیست.[2][3][4]
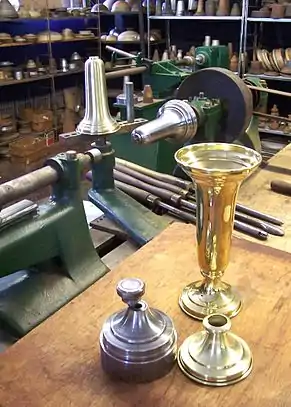
با توجه به این که در پرسکاری یا کشش عمیق، همواره هزینهٔ زیاد ابزار و قالب نکتهٔ مهمی است، اسپینینگ به عنوان فرایندی اقتصادی، کارا و با قابلیتهای فراوان، به عنوان روشی جایگزین و قابل قبول در تولید دستهای و محدود قطعات مطرح است. از سوی دیگر وقتی نیاز باشد قبل از تولید انبوه، نمونههایی برای انجام آزمایش تولید گردد، میتوان از این روش برای ساخت نمونههای اولیه استفاده نمود. قطعاتی با قطرهای ۶٫۴ تا ۷۹۰۰ میلیمتر و تا ضخامت ۷۶ میلیمتر را با روش اسپینینگ میتوان شکل داد.[3]
تاریخچه شکل دهی چرخشی
اسپینینگ (SPINNING)[6] یکی از قدیمیترین فرایندهای تولید محدود و دستهای برای قطعات متقارن توخالی و فلزی است که به نحو چشمگیری اقتصادی و ارزان میباشد. بنا بر مدارک و اسناد تاریخی، اسپینینگ فلزات از روزگار مصریان باستان شناخته شده بود و برای ساخت بشقابهای نقره ای از آن استفاده میشد. اما گفته میشود که پایههای اصلی صنعت اسپینینگ فلزات در ابتدای قرن دهم میلادی توسط چینیها بنا نهاده شد. از آن زمان سالهای زیادی گذشت تا این فرایند به جهان غرب آورده شد. این صنعت برای اولین بار در زمان سلطنت ادوارد سوم وارد انگلستان شد و پس از یک دورهٔ پانصد ساله، در حدود سال ۱۸۴۰ میلادی فردی به نام جردن این صنعت را به آمریکا برد.
در ابتدا این فرایند توسط دستگاههای سادهای انجام میگرفت که به علت دستی بودن هدایت ابزار، نقش اپراتور در آنها بسیار مهم بود و اپراتور باید مهارت زیاد و تجربهٔ طولانی در این کار میداشت.
طی سالهای متمادی فرایند اسپینینگ فلزات، بدون تغییر باقی ماند. در آن سالها اصولاً از فلزات نرم مانند آلومینیم و مس آن هم با ضخامتهای کم برای اسپینینگ استفاده میشد و فلزات سخت و ورقهای ضخیم را نمیتوانستند توسط اسپینینگ شکلدهی نمایند. کمکم با گسترش نیاز صنعت به قطعات مدور توخالی و دقیق تر از نظر ابعادی، این فرایند نیز روند تکاملی خود را طی نمود. متعاقباً در طراحی دستگاههای اسپینینگ، وظیفهٔ هدایت ابزارهای شکلدهی به جای دست اپراتور به عهدهٔ تجهیزات مکانیکی گذاشته شد و به این ترتیب اولین پایههای نوع جدیدی از این فرایند به نام اسپینینگ ماشینی یا قدرتی گذاشته شد. به وسیلهٔ این فرایند، امکان اسپینینگ فلزات سختتر با ضخامتهای بیشتر به وجود آمد.[7][8]
امروزه بیشتر تجهیزات و ماشین آلاتی که برای تولید قطعات دقیق در صنایع به کار میروند، به کنترلکنندههای عددی، با قابلیت برنامه پذیری پیشرفته مجهز شدهاند. در طول سالهای اخیر فرایند اسپینینگ بهطور همزمان در چندین کشور از جمله سوئد، آلمان، انگلستان، ژاپن و ایالات متحده آمریکا توسعهٔ فراوانی یافت و در پی آن روشهای دیگری از آن، مانند شکلدهی برشی یا شیر فرمینگ (Shear forming)[9] و اسپینینگ لوله یا فلو فرمینگ معرفی شدند.
با پیشرفت شگفتانگیز موتور توربین گازی هواپیماها، نیاز به فرایندهای اسپینینگ و فرایندهای مرتبط با آن برای تولید قطعات مختلف بیش از پیش احساس شد و این مسئله عامل بسیار مهمی در پیشرفت و توسعهٔ این فرایندها شد. دقت ابعادی قطعات تولیدی و اقتصادی بودن این روش دو عامل بسیار مهم در گسترش گرایش به استفاده از آن در صنایع مختلف، به ویژه در صنایع فضایی بود. متقابلاً به علت اهمیت این صنایع، گسترش و توسعه فرایندهای اسپینینگ روند فزایندهای پیدا کرد. امروزه با حساس شدن نقش اقتصاد در معادلات جهانی، استفاده از این فرایندها در سایر صنایع نیز رو به افزایش است. به عنوان مثال بسیاری از قطعات خودروها نیز، مانند قطعاتی از کلاچ یا رینگ خودرو توسط این فرایندها تولید میشوند[3][4]
مزایا و معایب
مزایای روش شکلدهی چرخشی نسبت به سایر روشهای شکل دهی:
- تولید بدون براده، بدون درز و سرد
- بهبود خواص ماده مثل استحکام تسلیم، عمر خستگی
- قابلیت تولید قطعات با ابعاد مختلف
- عدم نیاز به عملیاتهایی همچون ماشین کاری، سنگ زنی و …
- اقتصادی بودن آن در مقایسه با سایر روشها
- دقت ابعادی مطلوب قطعات تولیدی
در چند سال اخیر بر تنوع و گستردگی استفاده از این فرایندها به خصوص در صنایع پیشرفته و صنعت خودروسازی برای شکلدهی قطعات فلزی در سیستمهای تولید انبوه و نمونه سازی افزوده شدهاست. امروزه بیشتر ماشین آلات این فرایند با قابلیتهای برنامهریزی پیشرفته مجهز شدهاند.
دستهبندی روشهای چرخشدهی
روشهای اسپینینگ بر حسب عوامل مختلف دستهبندیهای گوناگونی دارد. با توجه به نوع دخالت انسان این فرایند به دو دسته اصلی سنتی (دستی) و ماشینی تفکیک میشود. به نحوی که در اسپینینگ دستی، نیروی تغییر شکل توسط اپراتور اعمال میشود ولی در روش ماشینی، نیروی تغییر شکل به وسیلهٔ ابزارهای مکانیکی و هیدرولیکی اعمال میگردد که به آن اسپینینگ قدرتی نیز گفته میشود.
فرایند اسپینینگ از جنبهٔ تغییر ضخامت در طی شکلدهی به دو دسته قابل تقسیم است. روشهایی که در اثر آن تغییر ضخامت بلنک یا پریفرم غیر محسوس بوده و با تجهیزات دستی و ماشینی قابل انجام اند و روشهایی که ضخامت قطعه کار در طی فرایند به نحو چشمگیری تغییر نموده و فقط از طریق اسپینینگ قدرتی یا تجهیزات ویژه قابل انجام هستند. شیر فرمینگ(Shear Forming) و فلو فرمینگ(Flow Forming) جزو دستهٔ دوم طبقهبندی میشوند.
در روش اسپینینگ از نظر دمای فرایند، نوع دیگری از طبقهبندی نیز وجود دارد، که با عناوین داغ و سرد شناخته میشوند. اغلب عملیات اسپینینگ بدون حرارت دهی به قطعه کار انجام میشود. البته این همیشگی نبوده در برخی موارد (در ضخامتهای زیاد) به منظور کاهش شکنندگی و تردی، قطعه کار گرم میشود.[6][10][3]
اسپینینگ دستی (سنتی)
در این روش تغییر شکل با مکانیزم خمکاری انجام میشود و در آن ضخامت، تغییر محسوسی نمیکند. این عملیات با استفاده از دستگاههایی مشابه دستگاه خراطی یا دستگاه راش قابل انجام است. در این روش ورق دایرهای شکلی که بلنک (BLANK) نامیده میشود، بین یک مندرل چرخان و مرغک دستگاه قرار میگیرد. نیروی فشار دست روی ابزار اهرم مانندی اعمال میشود که به تدریج پس از چندین مرحلهٔ کاری، فلز را روی مندرل خم میکند.[3][10]
اسپینینگ ماشینی
اسپینینگ ماشینی یا قدرتی از همان اصول اسپینینگ دستی بهره میگیرد با این تفاوت که به جای استفاده از نیروی بازوی اپراتور، از ابزارهای مکانیکی برای اعمال نیرو استفاده میشود. بخشی از تجهیزات و ابزار متعارف که برای انجام فرایند چند مرحلهای اسپینینگ سنتی به صورت ماشینی، تنظیم شدهاند عبارتند از:
- بلنک یا گرده اولیه (Blank): به شکل دایرهای از ورق تخت تهیه شده و در وضعیت هم مرکز با اسپیندل و مندرل قرار میگیرد بهطوریکه برای جلوگیری از پرتاب شدن در هنگام چرخش سریع، با نگهدارنده دستگاه به خوبی کلمپ میشود.
- غلتک اسپینینگ (Roller): در حالی که قطعه کار به سرعت دوران میکند، غلتک دستگاه طی چند مرحله برای شکلدهی به محصول در مسیرهای از پیش تعیین شده حرکت میکند. عامل چرخش غلتک، نیروی اصطکاک بین سطح قطعه کار و غلتک است.
- مندرل (Mandrel): قالبی است که بلنک در طی عملیات اسپینینگ روی آن مینشیند.
- تکیه گاه و نگهدارنده که بلنک را بر روی مندرل فشرده و ثابت میکند.
- زیر سری: با هدف جلوگیری از خم شدگی و انحراف ناخواسته و بیش از اندازه بلنک در طول عملیات اسپینینگ به کار میرود.
- ابزار برشی اندازهکننده: لبه قطعه کار پس از آخرین مرحله خواه نا خواه، باید آرایش، تنظیم و سایز شود. مجموعه الحاقی برشی با حرکت کشویی و عمود بر قطعه کار، جهت آرایش و سایز لبه نهایی قطعه کار اندازه دلخواه را تأمین مینماید.
- اسپیندل اصلی دستگاه که مندرل بر روی آن نصب میشود.
- کشویی یا اسلایدر متقاطع که با زوایای قابل تنظیم، مجموعه غلتک و نگهدارندههای آن را به طرف قطعه کار رانده و در مسیر برنامهریزی شده حرکت میدهد. مسیر حرکت غلتک در صفحه مختصات X و Z برنامهریزی میشود.
- مجموعه پایه مرغک
- قطعه کار نهایی پس از عملیات اسپینینگ.[10]
اسپینینگ لوله (Flow forming) - (Tube Spinning)
فرایند اسپینینگ لوله (Tube Spinning)یا فلو فرمینگ (Flow forming) یکی از فرایندهای نوین و منحصر به فرد در شکلدهی فلزات برای تولید لولههای بدون درز جدار نازک با تلورانسهای دقیق، صافی سطوح بالا و خواص مکانیکی عالی میباشد.[6]
این فرایند بهطور گستردهای برای تولید لولههای بدون درز مورد نیاز در صنایع نظامی، موشکی و هوافضایی مورد استفاده واقع میشود، البته اخیراً از این روش برای تولید لوله در بعضی از صنایع غیرنظامی مانند خودروسازی نیز بهرهگیری میشود.
ابزارهای اصلی که در فرایند اسپینینگ وجود دارد شامل: یک ماندرل و یک یا بیشتر از یک غلتک که لوله را شکل میدهند و بهطور متقارن در روی قطعه کار قرار گرفتهاند. در این فرایند در حالی که قطعه کار استوانهای شکل که روی ماندرل قرار گرفتهاست، به همراه آن حول محور تقارن خود با یک سرعت زاویهای ثابت میچرخد، غلتکها روی قطعه کار با یک سرعت ثابت کم پیشروی میکنند. در اسپینینگ مستقیم، جهت جریان فلز در جهت حرکت غلتکها میباشد. در صورتی که در اسپینینگ معکوس جهت جریان فلز در خلاف جهت حرکت غلتکها میباشد.[2][10]
اولین تحقیقات در رابطه با فرایند اسپینینگ لوله توسط درج (سال ۱۹۵۴) و تاماست (سال ۱۹۴۰) صورت گرفت. تحقیق دیگری در زمینه نیروهای اعمالی در این فرایند توسط کوبایاشی و تامسون در سال ۱۹۶۱ در دانشگاه کالیفرنیا انجام گرفت. آنها سعی کردند نیروهای عملکردی این فرایند را با اعمال فرضیات سادهکنندهای به دو روش نواری و روش خط لغزش محاسبه نمایند اما تحلیل آنها دقیق نبود. تحقیقات بعدی در این زمینه توسط هایاما (سال ۱۹۶۶) و دریکانت (سال ۱۹۷۳) صورت گرفت که با توجه به انجام آزمایشهای تجربی در این زمینه و مقایسه نتایج تحلیل نظری با نتایج تجربی، این تحلیلها از دقت بیشتری برخوردار گردید، اما با توجه به اینکه مکانیزم تغییر شکل در این فرایند بسیار پیچیده است، با روشهای نظری نمیتوان توزیع تنش و کرنش دقیق را در ناحیه تماس غلتکها با قطعه کار را بدست آورد. با توسعه روشهای عددی و به ویژه روش اجزا محدود و نیز افزایش توان محاسباتی کامپیوترها در سالهای اخیر، میتوان از روش اجزا محدود برای بدست آوردن توزیع تنش و کرنش در ناحیه تماس غلتکها با قطعه کار و در نتیجه تعیین مکانیزم تغییر شکل در اینگونه فرایندها استفاده نمود.
در سالهای اخیر چندین نرمافزار برای تحلیل مسائل تغییر شکل بزرگ و پلاستیک تهیه شدهاست که از بین آنها میتوان به نرمافزار ABAQUS که بر پایه روش المان محدود بنا شدهاست، اشاره کرد. این بسته نرمافزاری از دو شبیهساز صریح و ضمنی تشکیل شدهاست.
_(14761513444).jpg.webp)
حل مسایل غیر خطی پیچیده با روش صریح معمولاً به صرفه تر بوده و علاوه بر زمان حل نسبتاً کم در مقابل روش ضمنی، دقت بهتری را نیز ارائه میکند. معمولاً در آزمایشها به دلیل ماهیت تغییر شکل گسترده و همچنین تماسهای پیچیده بین لوله و غلتکها، بسته نرمافزاری ABAQUS/Explicit به عنوان بهترین انتخاب مورد استفاده قرار گرفتهاست.
مزایا و معایب فرایند اسپینینگ لوله
فرایند اسپینینگ لوله از پیشرفتهترین روشهای شکلدهی لوله میباشد. این فرایند موجب تولید لولههای بدون درز با ضخامت نازک و دقیق و خواص مکانیکی عالی میشود.
علی رغم مزایا و ویژگیهای فرایند اسپینینگ لوله، این فرایند از فرایندهای پیچیده در شکلدهی فلزات میباشد که تحلیل مسائل مربوط به آن مانند طراحی هندسه غلتکها، تعیین نیرو و انرژی لازم برای شکلدهی لوله و پیشبینی توزیع تنش و جریان فلز کار چندان سادهای نیست.
در حل مسائل مربوط به فرایند اسپینینگ لوله چند روش نظری به کار گرفته شدهاست که در بعضی موارد نتایج نسبتاً خوب و قابل قبولی بدست آمدهاست. این روشها را میتوان در مورد تخمین نیرو و انرژی مورد نیاز برای این فرایند استفاده کرد، اما با توجه به پیچیدگی مکانیزم شکلدهی و محدودیتهای این روشها و نیز فرضیات اعمال شده در این راه حلها، امکان پیشبینی دقیق توزیع تنش و کرنش در قطعات در هنگام شکلدهی وجود ندارد.
کاربردها و محصولات اسپینینگ
- لوازم خانگی: بشقاب، قابلمه، دیگ، ظروف غذا
- ظروف تزئینی: جام، چلچراغ و …
- صنایع هوایی: محفظه ورودی هوای توربوجت
- صنایع نظامی: محفظه احتراق موتور موشک، بدنه برخی از موشکها، کلاهکهای آیرودینامیک برخی راکتها و بدنه برخی نازلها، لوله خمپارهاندازها
- صنایع خودرویی: انواع رینگ تایرها، پولیهای تسمه خودرو
- فرایندهای مونتاژی: اتصال کفی بشکهها و قوطیهای کنسرو، قطعات صنعتی مانند عدسیهای مخازن، کپسولهای مایع[10][7][3]
فرایند فرمدهی چرخشی
فرمدهی چرخشی (0Rotary Swaging)[12] یا آهنگری با استفاده از قالبهای چرخان، یک نوع خاصی از فرایندهای آهنگری شعاعی[13] است که در ساخت لولهها و شفتهای فلزی به کار میرود.[14][15] در نتیجهٔ حرکت نوسانی قالبها که در اثر ضربات متعدد ساچمههای محیطی به دست میآید، قطعه کاری که به ناحیهٔ فضای بین قالبها وارد شده، به صورت تدریجی تغییر شکل یافته که عموماً این تغییر شکل همراه با کاهش قطر است.
قالبهای مورد استفاده در این فرایند، از سه بخش تشکیل شدهاند:
بخش اول که در ورودی قالب قرار دارد، عبارت است از ناحیهٔ کالیبراسیون که در انتهای این بخش صفحهٔ خنثی (Neutral Plane) قرار دارد. یعنی پس از عبور متریال از این صفحه، در اثر ضربات شعاعی حرکت محوری رو به عقب ندارد.
ناحیهٔ دوم، بخش تغییر شکل است که در آن قطر قطعه کار کاهش یافته.
ناحیهٔ سوم که قطعه کار به قطر نهایی رسیده و تثبیت میگردد.
این فرایند برای ساخت محصولات متنوعی از آلیاژهای Al ,Cu ,Fe ,Ti به کار برده شدهاست.
انواع ماشین های فرم دهی چرخشی (Rotary Swaging)
به صورت کلی با توجه به نحوۀ حرکت ابزار و قطعه کار، سه نوع دستگاه Rotary Swaging وجود دارد:
1-در ماشین هایی که تنها سیستم داخلی می چرخد، رینگ خارجی (Outer Ring) ثابت بوده و شفت اصلی (Main Shaft) می چرخد. با استفاده از این ماشین ها، قطعات بلند و متقارن ساخته می شوند.
2-در نوع دوم، سیستم خارجی می چرخد. به گونه ای که در این ماشین ها در حالی که شفت اصلی ثابت است ، رینگ خارجی همراه با چرخش سبب ایجاد حرکت نوسانی می گردد. در ساخت قطعات غیر متقارنی که قطعه کار می بایست همراه با تکه های قالب بچرخد، از این نوع ماشین ها استفاده می شود.
3-رینگ خارجی و شفت اصلی هر دو می توانند با هم و در جهت مختلف بچرخند، در این صورت فرکانس سیستم افزایش می یابد.
روش های شکل دهی در فرآیند فرم دهی چرخشی (Rotary Swaging)
شکل دهی با استفاده از فرآیند Rotary Swaging به سه طریق انجام می شود:
1-فرم دهی چرخشی همراه با تغذیۀ قطعه کار (In-feed Swaging) : در این روش قطعه کار با سرعت ثابت به درون ناحیۀ شکل دهی، تغذیه می شود.
2-فرم دهی چرخشی با حرکت شعاعی قالب (Recess Swaging) : پس از اینکه قطعه کار در مکان از پیش تعیین شده قرار گرفت در اثر حرکت شعاعی تکه های ابزار (علاوه بر حرکت نوسانی)، شکل دهی قطعه کار صورت می پذیرد.
3-فرم دهی چرخشی با استفاده از ماندرل: این شیوه، هم می تواند با روش In-feed و هم Recess انجام گیرد. به صورتی که قبل از اجرای فرآیند، یک ماندرل درون لوله قرار گرفته سپس مرحلۀ شکل دهی اجرا می گردد. [16]
شکل دهی لوله با استفاده از فرآیند فرم دهی چرخشی
شکل دهی لوله با استفاده از فرآیند فرم دهی چرخشی به هر دو صورت In-feed و Recess انجام می شود.[17]
ساخت اجزاء هوشمند (Smart Structures) با استفاده از فرآیند فرم دهی چرخشی
با استفاده از فرآیند فرم دهی چرخشی می توان پروسه های شکل دهی و اتصال را به طور همزمان انجام داد(Conjoint Forming). نمونه ای از این فرآیند، کاهش قطر یک شفت توخالی به همراه اتصال یک سنسور هوشمند جهت کنترل بارهای وارد شده بر شفت می باشد.
[18]
پوشش دهی فلزات ( Plating) با استفاده از فرآیند فرم دهی چرخشی
هدف اصلی از این فرآیند ساخت قطعاتی با ترکیب مواد مقاوم به خستگی در لایۀ درونی به همراه قطعات سخت، مقاوم به خوردگی و با ضریب اصطکاک پایین در لایۀ خارجی می باشد.[19]
اثر فرایند فرم دهی چرخشی بر استحکام و مقا ومت به خوردگی آلیاژهای منیزیم
ایمپلنتهای قابل تجزیه در بدن، یکی از شاخههای جدید در علم بیو مواد هستند که به تازگی، تحقیقات گستردهای در رابطه با آنها در حال جریان است. به تازگی منیزیم و آلیاژهایش در این دسته جای گرفتهاند. منیزیم به علت سمی نبودن، تطابق بسیار خوبی باشرایط بدن داشته و بهطور طبیعی در بافت استخوان وجود دارد. منیزیم قابلیت حلالیت در بافتها را داشته و بهطور همزمان در رشد بافت جدید نیز اثر گذار است. تحقیقات زیادی در زمینهٔ پوشش مواد زیست خنثی مثل Ti-6Al-4V با آلیاژ منیزیم، جهت ایجاد بافت استخوانی در جریان است. به عنوان مثال، پیوند نفوذی منیزیم و آلیاژهایش برروی آلیاژ Ti-6Al-4V به همراه Zr، که منجر به ایجاد ساختاری هیبریدی گردیدهاست. علاوه بر این، کاربرد منیزیم به عنوان بیرینگ افزایش یافته که به دلیل ویژگیهای منیزیم و آلیاژهایش است که تطابق و شباهت زیادی به رفتارهای استخوان دارند. یعنی پس از مجاورت ایمپلنت با استخوان، در اثر مرور زمان از چگالی استخوان کاسته نخواهد شد. ( (Stress Shielding Effect با این وجود به علت خوردگی بالای آلیاژ منیزیم بعد از ۱۸–۱۲ هفته، یکپارچگی مکانیکی آن از بین رفته، در حالی که در (طی این زمان بهبود بافت آسیب دیده امکانپذیر نیست. تلاشهای زیادی در راستای بهبود مقاومت به خوردگی از طریق آلیاژسازی یا ایجاد پوشش برروی آلیاژهای منیزیم، صورت گرفتهاست.این فرایند سبب کاهش اندازهٔ دانه و نتیجتاً افزایش استحکام این آلیاژها گردیدهاست. در یک بررسی برای افزایش استحکام آلیاژ WE43 که به عنوان ایمپلنتهای فناپذیر در بدن کاربرد دارند، از فرایند RS استفاده گردیدهاست. در این تحقیق آلیاژ ذکر شده تحت دو رژیم تغییر شکل با نسبتهای تغییر شکل مختلف و در دماهای متفاوت، به وسیلهٔ فرایند RS تحت تغییر شکل قرارگرفته است. قبل از اجرای فرایند بیلت اکسترود شدهٔ اولیه به مدت ۸ ساعت در دمای ۵۲۵ درجهٔ سانتی گراد، همگن شدهاست. بر اساس نتایج به دست آمده در بررسی ریز ساختار آلیاژ تغییر شکل داده شده، فرایند RS سبب کاهش اندازهٔ دانه بهطور قابل ملاحظه ای گردیده، به گونه ای که میانگین اندازهٔ دانه پس از دو رژیم تغییر شکل به ترتیب برابر با ۰٫۰۲±۰٫۶۶ میکرو متر و ۰٫۰۲±۰٫۶۱میکرومتر گزارش شدهاند. در حالی که میانگین اندازهٔ دانهٔ اولیه قبل از تغییر شکل برابر با ۵٫۹±۶۱٫۳ میکرومتر بودهاست. مقایسهٔ ویژگیهای مکانیکی قبل وبعد از تغییر شکل نشان داد که فرایند RS اثر قابل توجهی بر خواص مکانیکی آلیاژ WE43 داشتهاست. نقاط تسلیم، شکست و حداکثر تغییر طول آلیاژ WE43 قبل و بعد از فرایند، در جدول زیر درج گردیدهاند. (µ=ln(A0/Af علاوه بر این، کاهش دما سبب افزایش استحکام آلیاژ گردیدهاست به گونه ای که فازها نیز به صورت پراکنده تری توزیع شدهاند.[20]
%,El | UTS,MPa | YS,MPa | State of Alloy |
---|---|---|---|
۹ | ۲۳۴ | ۱۶۱ | Initial State |
۱۵٫۵ | ۳۳۶ | ۲۲۰ | T=۴۰۰°C , µ=۱٫۷۸ |
۱۲٫۵ | ۳۳۹ | ۲۶۰ | (T=۳۵۰°C , µ=2.78 (Regime ۱ |
۷٫۲ | ۴۱۶ | ۲۸۷ | (T=۳۲۵°C , µ=2.56 (Regime ۲ |
مقاومت به خوردگی آلیاژ WE43 که تحت فرایند RS قرار گرفته، تغییر چندانی نکردهاست. عموماً مقاومت به خوردگی فلزاتی که تحت تغییر شکل پلاستیک قرار میگیرند، کاهش مییابد. دلایل آن عمدتاً عبارتند از: افزایش طول مزردانهها و چگالی نابه جاییها، همچنین ایجاد دوقلوییهایی که پس ار تغییرشکل پلاستیک شدید در ریزساختار ایجاد میگردند. با این وجود آزمایش اخیر در مورد آلیاژ WE43 تصویر پیچیده تری را ارائه دادهاست. همان گونه که ذکر گردید، در بعضی از موارد استفاده از ایمپلنت به جای بافت استخوانی، پدیدهٔ Stress Shielding Effects یا اثر محافظت تنشی اتفاق میافتد. به گونه ای که به دلیل تفاوت مدول الاستیک استخوان با ایمپلنت، تمام بار وارده بر استخوان توسط ایمپلنت تحمل شده و بافت استخوانی به مرور از بین رفته و جذب شده و منجر به از بین رفتن مکان استقرار ایمپلنت میگردد. یکی از راه حلها برای رفع این مشکل، استفاده از موادی با مدول الاستیک نزدیک به استخوان است. علاوه بر این، مقاومت به خوردگی ایمپلنت در محیط بدن نیز بسیار با اهمیت است. به عنوان نمونه افزایش منیزیم معادل درکامپوزیت بی متال Ti-Mg به عنوان ایمپلنت باعث میشود که مدول الاستیک آن پایین آمده و در حوزهٔ مدول الاستیسیتهٔ استخوانهای اسفنجی قرار گیرد. همچنین کاهش چگالی شدت جریان با افزایش منیزم معادل حاصل از نتیجهٔ آزمایش مقاومت به خوردگی به صورت in-Vitro، حاکی از افزایش مقاومت به خوردگی است. مضافاً تولید اکسید منیزیم و هیدروکسید منیزیم به صورت پوسته بر روی سطح پودرهای منیزیم در کامپوزیت، از دیگر دلائل این موضوع میباشند. نهایتاً، وجود مرزدانههای طولانی از آلیاژهای منیزیم سبب جلوگیری از خوردگی حفره ای گردیده و توزیع فازهای ثانویه به صورت یکنواخت، (در این مورد اینتر متالیک غنی از فلزات نادر خاکی) نیز در این زمینه اثرگذار میباشند. در این بررسی جهت ساخت این کامپوزیت علاوه بر روش متالورژی پودر، برای افزایش چگالی، کاهش تخلل و زینتر شدن بهتر ذرات پودر، از فرایند RS گرم استفاده گردیدهاست.[21]
جستارهای وابسته
- فرایندهای شکلدهی
- تئوری پلاستیسیته
- الاستیسیته
- فلزکاری
پیوند به بیرون
- ساخت میهن
- پژوهشگاه علوم و فناوری اطلاعات ایران
- http://www.centurymetalspinning.com/
منابع
- Black, J.T. (2011). DeGarmo's Materials and Processes in Manufacturing. Wiley; 11 edition. pp. 457, 458. ISBN 978-0470924679.
- Black, J.T. (2011). DeGarmo's Materials and Processes in Manufacturing. Wiley; 11 edition. pp. 457, 458. ISBN 978-0470924679
- Helander. "Metal Spinning". Retrieved 2016-11-08.
- C.C. Wong, T.A. Dean, J. Lin: A review of spinning, shear forming and flow forming processes, International Journal of Machine Tools & Manufacture (2003)
- https://en.wikipedia.org/wiki/Metal_spinning#/media/File:Metal_spinning_brass_vase.jpg
- Metal Spinning
- PMF Industries, Inc. Precision Metal Forming, 2601 Reach Road P.O. Box 3186 Williamsport, Pennsylvania 17701 USA, www.pmfind.com
- Century Metal Spinning Co. Metal spinning Workshop P O Box 1084, North Wales, PA 19454, http://www.metalspinningworkshop.com/
- Shear forming
- http://www.iran-mavad.com
- پرونده:Metal spinning (1912) (14761513444).jpg
- آشنایی با آهنگری سرد یا فرم دهی چرخشی
- "Radial Forging | Metalworking: Bulk Forming | Handbooks". dl.asminternational.org. Retrieved 2019-06-22.
- "Rotary Swaging". www.metalltechnik-menges.de. Retrieved 2019-06-22.
- "Forming characteristics of tubular product through the rotary swaging process". ResearchGate. Retrieved 2019-06-22.
- Görtan، Mehmet. , Severe plastic deformation of metallic materials by equal channel angular swaging: Theory, experiment and numerical simulation.
- Q. Zhanga, K. Jina, D. mua, P. Mab, J. Tianc. «, Rotary swaging forming process of tube workpieces».
- M. Krech, A. Trunk, P. Groche. «Controlling the sensor properties of smart structures produced by metal forming».
- V. Şchiopu, D. Luca. «A new net-shape plating technology for axisymmetric metallic parts using rotary swaging».
- «Strengthening of Magnesium Alloy WE43 by Rotary Swaging». Materials Science Forum.
- «Titanium–magnesium based composites: Mechanical roperties and in-vitro corrosion response in Ringer's solution». Materials Science & Engineering A.