ماشینکاری پرتو الکترونی
ماشین کاری پرتو الکترونی (به انگلیسی: Electron Beam Machining) به صورت مخفف (EBM) یکی از روشهای نوین ماشینکاری و البته یک فرایند حرارتی محسوب میشود که از پرتوهای الکترونی پر انرژی متمرکز شده برای ایجاد چگالی توان بسیار بالا بر روی سطح قطعه کار استفاده میکند و بدین وسیله تبخیر یا ذوب آنی ماده قطعه کار را سبب میشود. در این روش ماشین کاری از یک ولتاژ بالا که معمولاً تا ۱۲۰ کیلوولت است، برای شتاب دادن به الکترونها با سرعتی در حدود ۵۰ تا ۸۰ درصد سرعت نور استفاده میشود. برخورد پرتو الکترونی با قطعه کار تولید پرتو X میکند که بسیار خطرناک و مضر است؛ بنابراین حفاظت و پوشش ضروری بوده و میبایست از پرسنل با مهارت کافی جهت استفاده از تجهیزات بهره برد. EBM میتواند برای مواد رسانا و نارسانا استفاده شود. خواص ماده نظیر چگالی، رسانایی الکتریکی و حرارتی، انعکاس و نقطه ذوب معمولاً عوامل محدودکننده این فرایند محسوب نمیشوند. بیشترین کاربرد EBM در صنعت، دریل کاری دقیق سوراخهای کوچک از گستره ۰٫۰۵ تا ۱ میلیمتر است.
مبانی فیزیکی فرایند
در این روش، انرژی جنبشی الکترونهای به حرارت تبدیل میشود و سبب افزایش درجه حرارت قطعه کار که بالاتر از نقطه جوش آن است، میشود و این سبب میشود تا براده برداری به صورت تبخیری صورت گیرد. با توجه به شدت قدرت 1.55MW/mm2 که در این روش رخ میدهد، تمام مواد مهندسی را میتوان ماشین کاری کرد.
نحوه نفوذ موج متمرکز شده و اینکه چگونه به داخل قطعه نفوذ میکند، به دلیل پیچیدگی مکانیزم آن، کاملاً مشخص نیست؛ اما اعتقاد بر این است که سطح قطعه کار به وسیله ترکیب فشار الکترون و کشش سطحی ذوب میشود. ماده مذاب به سرعت خارج و تبخیر میگردد و در نتیجه، نرخ براده برداری در حدود ۱۰ میلیمتر مکعب بر دقیقه را به وجود میآورد. موج الکترون پالسی با فرکانس ۱۰۰۰۰ هرتز سبب کاهش درجه حرارت قطعه کار در خارج از منطقه ماشین کاری میگردد.
تجهیزات EBM
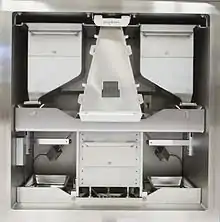
اجزاء ماشین EBM درون محفظهای قرار دارد که توسط یک پمپ، شرایط خلاء در آن برقرار میشود. از پتانسیل ولتاژ بالا برای شتاب دادن الکترونها از کاتد (فیلامنت) که از جنس تنگستن میباشد به سمت حفره آند استفاده میشود. الکترونها از رشته تنگستنی داغ ساطع میشود. کاتد تنگستنی تا حدود ۲۵۰۰ درجه سانتی گراد برای ساطع کردن الکترون حرارت داده میشود. معیار مناسب بودن مقدار الکترون ساطع شده، شدت جریان میباشد که باید بین ۵ تا ۱۵ آمپر در سانتیمتر مربع باشد. جریان ساطع شده به جنس کاتد، درجه حرارت و ولتاژ بالا بستگی دارد که معمولاً در حد ۱۲۰ کیلوولت است. پس از شتاب گیری، الکترونها به وسیله میدان متمرکز شده از سوراخ آند میگذرند. موج الکترون سپس به وسیله یک سیستم لنز مغناطیسی مجدداً متمرکز میگردد و در نتیجه موج الکترون به سمت قطعه کار هدایت میشود. لنز مغناطیسی برای متمرکز کردن پرتو به یک نقطه با گستره قطر ۱۲ تا ۲۵ میکرومتر استفاده میشود، همچنین از یک کویل انحنادار برای منحرف کردن پرتو به زوایای کمتر از ۵ درجه استفاده میشود. با توجه به این انحراف میتوان شکلها و ساختارهای استانداردی را ایجاد کرد.
الکترونهای شتاب دار با سرعت ۲۲۸۰۰۰ کیلومتر بر ثانیه در یک سطح تعیین شده به قطر ۰٫۲۵ میلیمتر به سطح قطعه کار برخورد میکنند.
پارامترهای فرایند
پارامترهایی که بر کارایی EBM اثر میگذارند عبارتند از:
- چگالی و خواص حرارتی قطعه کار (فیلتر گرمایی ویژه، رسانایی حرارتی و نقطه ذوب)
- ولتاژ شتاب دهنده
- تداوم پالس
- فرکانس پالس
- قطر تمرکز پرتو
- سرت جا به جایی قطعه کار
یکی از ویژگیهای مهم EBM، نرخ برداشت کوچک آن که در بیشترین حالت به ۰٫۱ سانتیمتر مکعب بر دقیقه میرسد. این مقدار با افزایش انرژی پالس افزایش مییابد. قابلیت ماشین کاری قطعه به دمای ذوب آن بستگی دارد. بهطوریکه قطعات نازک و کادمیومی بالاترین قابلیت ماشین کاری را دارند، در حالی که تنگستن و مولیبدن در این روش از قابلیت ماشین کاری پایینی برخوردارند. در فرایند دریل کاری با پرتو الکترونی تلرانسهای در دسترس بستگی به قطر سوراخ و ضخامت قطعه کار دارد؛ در حالیکه صافی سطح به انرژی پالس بستگی دارد. بسته به شرایط قطعه کار، تلرانس سوراخهای دریل شده در گستره مقادیری چون ۵ تا ۱۲۵ میکرومتر است. صافی سطح در گستره ۰٫۲ تا ۶٫۳ میکرومتر قرار میگیرد.
عمق نفوذ به قطر موج، شدت قدرت و ولتاژ بستگی دارد. علاوه بر آن، عمق ماده برداشته شده به ازای هر پالس، به چگالی قطعه کار و قطر کار و قطر موج وابسته است. عملاً تعداد پالسهای لازم برای سوراخ کاری با عمق معین، با افزایش ولتاژ شتاب، کاهش مییابد. برای یک شرایط معین تنظیم پارامترها، تعداد پالسهای لازم به صورت هذلولی با افزایش عمق سوراخ، افزایش مییابد. این بدین معنی است که برای عملاً با رسیدن به یک عمق معین، عمیقتر کردن سوراخ نیاز به تعداد بسیار زیادتر پالس خواهد داشت. زمان ماشین کاری در EBM برای یک سوراخ معین، به تعداد پالسها و فرکانس آن بستگی دارد. برای شیار تراشی به وسیله EBM، زمان ماشین کاری، تابعی از طول شیار، قطر موج، زمان پالس و تعداد پالس لازم میباشد.
مزایای EBM
- دریل کاری با کیفیت مناسب سوراخها با نرخ بسیار بالا (تا ۴۰۰۰ سوراخ در هر ثانیه)
- ماشین کاری هر نوع ماده مستقل از خواصش
- ماشین کاری میکرو با صرفه اقتصادی و سرعتی بیشتر از فرایندهای ماشین کاری الکتروشیمیایی و ماشین کاری تخلیه الکتریکی
- دارای دقت و قابلیت تکرارپذیری بالا برای مکان سوراخ (دقت ۰٫۱ میلیمتر) و قطر سوراخهای دریل شده (دقت ۵ درصد قطر سوراخ)
- قابلیت تغییر آسان پارامترهای ماشین کاری حتی در زمان ایجاد سوراخها به صورت سطر به سطر
- ایجاد بهترین سطح پرداخت در مقایسه با سایر فرایندها
- قابلیت تولید و اتوماسیون با مرتبه بالا
- قابلیت ایجاد زوایای تیز
محدودیتهای EBM
- قیمت بسیار زیاد تجهیزات
- اتلاف زمانی زیاد در زمان تخلیه محفظه ماشین کاری
- نیاز به مهار قطعه کار
- نیاز به نیروی کار ماهر و آشنا به برنامهنویسی CNC و خطر اشعه X
کاربردهای EBM
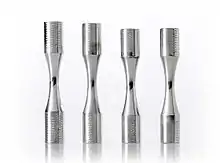
EBM معمولاً در دریل کاری و عملیات آهن بری استفاده میشود. به خصوص زمانی دریل کاری توصیه میشود که سوراخهای کوچک زیادی باید ایجاد شود یا به خاط هندسه قطعه کار و سختی آن، دریل کاری آنها مشکل است. به خصوص در صنایع نساجی و شیمیایی از EBM به منظور تولید تعداد زیادی سوراخ در فیلترها و توریهای سیمی استفاده میشود.
جستارهای وابسته
منابع
- https://www.ptreb.com/electron-beam-welding-information
- DeGarmo's Materials and Processes in Manufacturing By Degarmo, J. T. Black, Ronald A. Kohser
- https://en.wikipedia.org/wiki/Electron_beam_machining
- https://me-mechanicalengineering.com/electron-beam-machining-ebm
- Fundamentals of Machining Processes: Conventional and Nonconventional Processes By Hassan Abdel-Gawad El-Hofy
مشارکتکنندگان ویکیپدیا. «Electron beam machining». در دانشنامهٔ ویکیپدیای انگلیسی.