شکلدهی انفجاری
شکلدهی انفجاری (به انگلیسی: Explosive forming) روشی است که در آن از ضربه انفجاری به جای پانچ یا فشار به منظور فرمدهی فلز استفاده میشود و از اواخر قرن هجدهم میلادی اختراع شد. گزارش شدهاست که اولین بار در سال ۱۸۷۸، توسط دانیل آدامسن در منچستر انگلستان استفاده شدهاست. در سال ۱۸۹۸ اولین پروانه ثبت اخراع شکلدهی انفجاری در انگلستان به شماره ۲۱۸۴۰ ثبت شد. به فاصله مدت کوتاهی بعد از آن، در سال ۱۹۰۹ ثبت اختراع به شماره ۹۳۹۷۰۲ در ایالات محده آمریکا در مورد این فرایند به ثبت رسید. در دهه ۵۰ میلادی شرکت موور (به انگلیسی: Moore Company) توانست به وسیله این فناوری بدنههای فنهای بزرگ را تولید کند. این نوآوری منجر به کاهش ۱۵ درصدی هزینه تولید نسبت به روشهای شکلدهی مرسوم آن دوره شد. تفاوت عمده این روش با روشهای دیگر شکلدهی فلزات در این است که ابتدا به فلز سرعت داده شده و با تبدیل انرژی جنبشی در آنها به انرژی پلاستیک، تغییر شکل صورت میگیرد. این تکنیک در مواردی که نسبت به روشهای مرسوم مزیت دارد نظیر هزینه ساخت و سادگی پیادهسازی، استفاده میشود. این روش به دو دسته انفجار سطح پایین و انفجار سطح بالا تقسیم میشود. تنش حاصله در فرمدهی نوع دوم تا نیز ممکن است برسد.
نکته منحصر به فرد این گونه روشهای فرمدهی، فشار بسیار بالایی است که در اثر برخورد دو جسم صلب با سرعت زیاد به وجود میآید. فهم دقیق این مطلب نیازمند مطالعه رفتار موجی درون اجسام جامد میباشد.
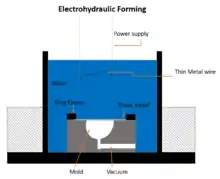
روشهای مختلفی برای انجام این کار وجود دارد، یکی از آنها قرار دادن قطعه در مقابل یک قالب و انفجار بار در فاصله مناسب از آن میباشد. این فرایند یعنی فرمدهی الکتروهیدرولیک نوعی از فرمدهی فلزات میباشد که قوس تخلیه الکتریکی برای تبدیل انرژی الکتریکی به انرژی مکانیکی استفاده میشود. یک بانک خازنی یک پالس جریان بالا را به دو الکترود، که در فاصله کمی از هم قرار دارند و در یک مایع نظیر آب یا روغن قرار دارند، انتقال میدهد. قوس جریان به سرعت سیال اطراف را تبخیر کرده که منجر به تولید ضربه موج میشود. قطعه مورد نظر، که در تماس با سیال قرار دارد، با برخورد به قالب شکل میگیرد. یکی دیگر از روشهای مشابه شکلدهی انفجاری، شکلدهی الکترومغناطیسی است که با استفاده از میدان مغناطیسی درون قطعه یک جریان الکتریکی ایجاد میکند که جریان ایجاد شده نیز باعث ایجاد یک میدان مغناطیسی مخالف با میدان اول میشود. برآیند این دو نیرو باعث شکلدهی به فلز میشود. در واقع میتوان فرمدهی الکتروهیدرولیک را پلی میان شکلدهی انفجاری و شکلدهی الکترومغناطیسی دانست.
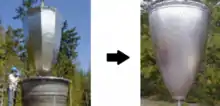
تاریخچه فرمدهی انفجاری
قابلیت اجرایی این روش در دهه ۵۰ میلادی ارائه شد و اوائل دهه ۶۰ میلادی برای صنایع هواپیمایی اولین طرح عملیاتی آن به اجرا رسید. در دهه ۶۰ میلادی حداقل ۸۰ پروژه فضایی تحت حمایت دولت آمریکا همزمان در حال انجام بود. تنها سازمان فضایی ایالات متحده آمریکا (به انگلیسی: NASA) علاقهمند به تحقیق در این حوزه نبود، بر اساس گزارش پژوهشی منتششر شده از اداره تحقیقات پیشرفته نظامی آمریکا(به انگلیسی: DARPA) در اواسط دهه ۶۰ میلادی، شکلدهی انفجای از پروژههای این سازمان بودهاست. در نتیجه این پروژه پیشرفت قابل توجهی در زمینه شکلدهی فلزات با دقت بالا، اشکال پیچیده، اندازههای بزرگ و هزینه مقرون به صرفه شد. از کاربردهای این پروژه در وزارت دفاع ایالات متحده میتوان به ساخت حلقه پسسوز موتور جت SR-71، کلاهک موشکهای قارهپیما و بدنه هواپیماها را نام برد. تلاشهایی از این دست فقط معطوف به ایالات متحده آمریکا نشد، در همان بازه زمانی اقداماتی در بریتانیای کبیر در دانشگاههای منچستر و کویینز (به انگلیسی: Queens University)انجام شد. فرق عمده این تکنیک با دیگر روشهای فرمدهی انفجاری منبع انرژی آن است؛ که در مقام مقایسه به بانک خازنیهای بزرگ نسبت به منابع انرژی در اندازه متوسط تر لازم است. این مسئله این روش را بزرگتر و پرهزینهتر میسازد. اما در طرف مقابل این روش به عنوان مثال در صنعت اتومبیلسازی به علت کنترل دقیقتر و تخلیه انرژیهای متوالی و کوچکی محیط الکترود و سیال، انتخاب مناسبی بود. این روش به دو شکل بدون قالب و فرم دهی توسط قالب صورت میگیرد. فرمدهی بدون قالب برای ایجاد شکم برای شکلهای دایرهای به کار میرود. به علت نبود قالب دقت این روش پایین است.
تجهیزات به کار گرفته شده در این روشها میتواند از جنس فایبرگلاس برای فرایندهای کوتاه مدت یا بتن برای قسمتهای بزرگتر در مدت زمانی بیشتر، یا آهن برای کارهایی با فشار لازم بالا، ساخته شود. در عمل نقطه تسلیم این ادوات باید از نقطه تسلیم قطعه مورد نظر برای شکلدهی باشد. در این روش شکلدهی هزینه ماشینکاری ثانویه بسیار پایین میباشد.
ماده منفجره
اینها موادی هستند که واکنش سریع شیمیایی را که در طی آن گرما و تعداد زیادی از محصولات گازی گسترش مییابند، تحمل میکنند. مواد انفجاری میتوانند در حالت جامد (TNT – three nitro toluene)، مایع (نیتروگلیسیرین)، یا گاز (اکسیژن و مخلوطهای استیلن). مواد انفجاری به دو دسته تقسیم میشوند: low explosiveها که در آنها سوختن ماده انفجاری نسبت به انفجار سریع تر رخ میدهد و از این رو فشار زیادی به وجود نمیآید، و high explosiveها که دارای نرخ بالایی از واکنش با فشار بالا دارند. از low explosiveها به عنوان عوامل جلوبرنده و راننده در تفنگها، و راکتها برای جلوبری موشکها استفاده میشود.
از دیدگاه ماده انفجاری
برای ایجاد موج لازم جهت انفجار میتوان از مواد منفجره جامد (و یا مایع) استفاده کرد یا همچنین میتوان از مخلوز گازها جهت انفجار استفاده کرد. باید توجه داشت در صورت استفاده از مخلوط گاز باید تلاش شود که اجزای این مخلوط به نسبت استوکیومتری در واکنش احتراق با هم ترکیب شده باشند زیرا بهینهترین حالت شکلدهی در این شرایط اتفاق میافتد. از نکات دیگر قابل توجه تأثیر فشار مخلوط شدن دو گاز با یکدیگر میباشد، زیرا با تغییر این متغیر میتوان تأثیر را در قطعه شکل داده شده مشاهده کرد. استفاده از مخلوط گازها (مانند مخلوط گاز اکسیژن و هیدروژن) فوایدی زیر را به همراه دارند:
- خطر انفجار مخلوط گاز پایینتر است و در هر کارگاهی با امکانات ساده قابل پیادهسازی است.
- فشار نهایی حاصل از انفجار و همچنین تغییرات فشار اعمالی در مراحل انجام کار بهطور مستقل از یکدیگر قابل کنترل هستند
- اتوماتیک کردن مراحل استفاده از انفجار گاز راحتتر میباشد و تکرار فرایند بدون مشکل انجام میشود
- معمولاً مواد منفجره و تجهیزات مورد استفاده هنگام بکارگیری، در آب قرار میگیرند در حالیکه در مخلوط گازی نیازی به وجود آب نیست
- صدای تولید شده کمتر است.
- هزینه کمتری نیز مورد نیاز است.
مواد قابل استفاده در فرایند شکلدهی انفجاری
بیشتر فلزات مانند: آهن، فولاد، مس، آلومینیوم و سرب قابلیت استفاده در این فرایند را دارند. همچنین بسیاری از کامپوزیتهای پایه فلزی نیز قابلیت استفاده در این روش را دارند.
تیتانیوم و آلیاژهای آن بسیار سبک هستند و لذا برای صنایع هوافضا ایدهآل میباشند. این مواد بسیار سخت بوده و شکلدهی آنها دشوار است. اما به وسیله روش شکلدهی انفجاری با تلرانس دقیقی میتوان آنها را ساخت.[1]
جنس قالب
تنتخاب مواد قالبها را بر اساس چند فاکتور آنجا میشود که عبارتند از:
- زمان تولید
- تلرانس مورد نیاز قطعه پایانی
- نوع و ضخامت فلز در حال کار
- فاصله میانی
- وزن مواد منفجره
قالبهای غیر مستحکم عموماً برای تولید در مقیاس کم و برای اجزایی با دقت نه چندان بالا استفاده میشود و قالبهای مستحکم تر غالباً برای تولید در مقیاس بزرگ مورد استفاده قرار میگیرند. برای ساخت این قالبها باید از فلزاتی با تنش تسلیم بالا استفاده نمود. مشکل دیگر آن است که اگز فلز دارای استحکام بالا باشد ممکن است ماشین کاری مطلوب آن برای شکل دهی، انحنای مناسب و در نهایت ساخت قالب مناسب، بسیار زمان بر و حتی غیرممکن باشد.
برای تولید در مقیاس کم و ساخت مدل معمولاً از کامپوزیتهایی مانند فایبرگلاس استفاده میشود. در جدول زیر برخی مواد رایج برای ساخت قالب و نیز کاربرد آنها را نشان میدهد.[2]
جنس قالب | کاربرد |
---|---|
بتن | فشارهای متوسط و تولید زیاد |
آهن چکش خوار | فشارهای بالا و تولید زیاد |
اپکسی و بتن | فشارهای کم وتولید زیاد |
فایبرگلس و بتن | فشارهای کم وتولید زیاد |
kirksite | فشارهای کم وتولید کم |
kirksiteو فایبرگلس | فشارهای کم وتولید کم |
منابع
<G. S. Daehn, High Velocity Metal Forming ASM Handbook, Volume 14B, Metalworking: Sheet Forming, Published 2006, pp. 405–418.>
<P. Dordizadeh B. and P. Gharghabi, “Dynamic Analysis of a Fast-acting Circuit Breaker (Thompson) Drive Mechanism” Journal of the Korean Physical Society, 59(61); p. 3547-3554, 2011.>
<https://www.fsb.unizg.hr/deformiranje/Explosive%20Forming%20of%20Metal.htm>
<https://www.engineeringclicks.com/explosive-forming/>
<http://doi.org/10.1016/S0924-0136(02)00413-2>
- 1. Rinehart J.S and Pearson, John, Explosive Working of Metals, Pergamon Press, 1963. New York.
- https://www.fsb.unizg.hr