ریختهگری با قالب دائمی
از شناخته شدهترین زیرشاخهٔ این شیوه، ریختهگری نیمه منجمد میباشد.
- پرکاربردترین فلزات در ریخته گری قالب دائم عبارتند از: آلومینیوم، منیزیم، آلیاژهای مس و سایر فلزات همچون قلع،روی، آلیاژهای سرب، آهن و استیل هم در قالبهایی از جنس گرافیت ریخته گری میشوند.
- معمولترین قطعاتی که با این روش تولید میشوند عبارت اند از: چرخ دنده، هزار خار، جعبه دنده، اسباب لوله کشی، محفظهٔ تزریق سوخت و پیستون موتور اتومبیل و…از محصولات ریخته گری با قالب دائمی
- ریخته گری با قالب دائم شامل مراحل زیر است:
ریختهگری با قالب دائمی
۱. آماده سازی قالب:
ابتدا خود فالب از قبل حرارت داده میشود تا دمای حدود ۳۰۰ – ۵۰۰ درجه فارنهایت، تا اجازهٔ جریان یافتن بهتر به فلز داده شود و کاستیها و نقصهای مربوط به قالب برطرف شود. سپس یک پوشش سرامیکی برای سطح حفره دار قالب به کار برده میشود تا هم فرایند جداسازی قطعه از قالب آسان تر شود هم اینکه عمر قالب افزایش یابد..
۲. مونتاژ فالب:
قالبها حداقل از ۲ قسمت تشکیل میشوند – یا ۲ قسمت با مرکزهایی دیگر برای تولید قطعاتی پیچیدهتر. مرکزها معمولاً از جنس آهن یا استیل هستند ولی گاهی از ماسهٔ قابل کاربرد هم استفاده میشود. در این مرحله مرکزها جاگزاری میشوند و دو نیمه در هم چفت میشوند..
۳. ریختن مذاب:
در این مرحله فلز مذاب توسط ملاقهٔ مخصوصی و به آرامی از طریق سوراخ راه گاه بالای قالب داخل قالب ریخته شده و وارد حفرهها میشود.
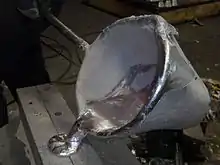
۴. خنک کردن:
به فلز مذاب درون قالب فرصت داده میشود تا خنک و جامد شود.
۵. بازکردن قالب:
بعد از طی مرحلهٔ جامد شدن، ۲ نیمهٔ قالب از هم باز میشوند و قطعهٔ منجمد شده را خارج میکنند.
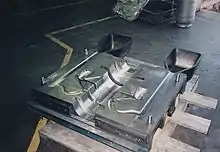
۶. پرداخت کاری قطعه:
در حین خنک کردن، فلز باقی مانده در راه گاه به قطعهٔ اصلی میچشبد و در این مرحله این چنین قسمتهای زایدی باید از قطعه جدا و کنده شوند.
- تعدادی از رایجترین فرایندهای ریخته گری با قالب دائم :
- تعدادی از رایجترین فرایندهای ریخته گری با قالب دائم :
۱. ریخته گری نیمه جامد:
این روش یک حالت ویژه از ریختهگری قالب دائم میباشد که در آن اجازه داده نمیشود تمام فلز مذاب منجمد شود، بلکه زمانی که ضخامت مورد نظر قطعه حاصل شد، فلز باقی ماندهای کاملاً منجمد نشده، از قالب بیرون ریخته میشود.
۲. ریخته گری کورتیاس:
در این روش از یک پیستون برای جمعآوری فلز مذاب داخل راه گاه استفاده میشود که روشی مناسب برای تولید قطعاتی با ضخامتهای کم و دارای جزئیات میباشد.
۳. ریخته گری تحت فشار:
در این روش به جای کمک گرفتن از جاذبهٔ زمین برای جاری شدن مذاب، از فشار حدود ۱ اتمسفر استفاده میشود. نگهداری فلز تحت این فشار باعث میشود که قالب بهطور کامل پر شود و هر میزان افتی در مرحلهٔ خنک کردن را متعادل نگه میدارد. خواص مکانیکی قطعهٔ تولید شده توسط این روش به نسبت روشهای سنتی، ۵ درصد برتری دارد..
۴. ریختهگری تحت خلاء":
این روش بسیار مشابه روش تحت فشار میباشد با این تفاوت که به جای استفاده از فشار، فلز مذاب را تحت خلاء قرار میدهند.
در هر ۲ روش تحت فشار و تحت خلاء، مادامی که تغذیه کنندهای استفاده نشود، بازده بالایی خواهیم داشت.در این روش نیز خلوص فلز به خوبی حفظ میشود و برتری خواص مکانیکی نسبت به روشهای سنتی حدود ۱۰ الی ۲۰ درصد میباشد.
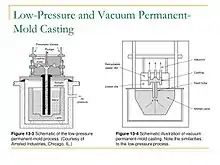
منابع
ttp://www.custompartnet.com/wu/permanent-mold-casting
http://www.efunda.com/processes/metal_processing/permanent_mold.cfm
<(Degarmo, E. Paul; Black, J. T. ; Kohser, Ronald A. (2003), Materials and Processes in Manufacturing (9th ed/>
<Kalpakjian, Serope; Schmid, Steven (2006), Manufacturing Engineering and Technology (5th ed.)/>