ساخت ادوات نیمرسانا
ساخت دستگاه نیمه رسانا فرایندی است که برای تولید دستگاه های نیمرسانا مورد استفاده قرار می گیرد ، معمولاً دستگاه های نیمه هادی فلز اکسید - نیمه رسانا (MOS) در تراشه های مدار مجتمع (IC) استفاده می شوند که در دستگاه های الکتریکی و الکترونیکی روزمره وجود دارند. این یک توالی چند مرحله ای ازمراحل پردازش فوتولیتوگرافیک و شیمیایی است (مانند غیرفعال ساری سطحی ، اکسایش حرارتی ، انتشار سطحی و جداسازی پیوند ) که طی آن مدارهای الکترونیکی به تدریج روی ویفر ساخته شده از مواد نیمه رسانای خالص، ایجاد می شوند.از سیلیکون تقریباً همیشه استفاده می شود ، اما از نیمرساناهای مرکب مختلف برای کاربردهای تخصصی استفاده می شود.
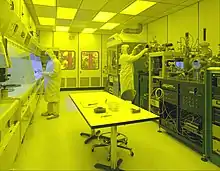
کل مراحل ساخت و تولید ، از ابتدا تا تراشه های بسته بندی شده آمادهی حمل ، شش تا هشت هفته به طول می انجامد و در کارخانه های کاملاً تخصصی ساخت نیمرسانا، که ریخته گری یا Fab نیز نامیده می شوند، انجام می شود. [1] تمام ساخت و سازها در داخل یک اتاق تمیز انجام می شود ، که قسمت مرکزی یک Fab است. در دستگاه های دیگر پیشرفته نیمرسانا، از جمله گرههای مدرن 14 / 10 / 7 نانومتری، ساخت می تواند تا 15 هفته طول بکشد ، با در نظر گرفتن 11-13 هفته متوسط صنعت. [2] تولید در تاسیسات پیشرفته ساخت کاملاً خودکار بوده و در یک محیط نیتروژن مهر و موم شده برای بهبود عملکرد (درصد ریز تراشه هایی که به طور صحیح در ویفر عمل می کنند) انجام می شود ، با سیستم های حمل و نقل اتوماتیک مواد که از حمل ویفر از ماشین به ماشین دیگر مراقبت می کنند. ویفرها به داخل جعبه های پلاستیکی مهر و موم شده FOUPs حمل می شوند. تمام ماشین آلات و FOUP ها حاوی جو نیتروژن داخلی هستند. هوای داخل ماشین آلات و FOUPs معمولاً تمیزتر از هوای اطراف در اتاق تمیز است. این فضای داخلی به عنوان یک مینی محیط نیز شناخته می شود. [3] کارخانه های تولیدی به مقدار زیادی نیتروژن مایع برای حفظ جو در داخل ماشین آلات تولید و FOUP ها که به طور مداوم با نیتروژن پاکسازی می شود ، نیاز دارند. [4]
ابعاد
یک فرایند نیمرسانا خاص دارای قوانین خاصی در مورد حداقل اندازه و فاصله برای ویژگی های موجود در هر لایه تراشه است. [5] غالباً یک فرآیند نیمرسانای جدید دارای حداقل اندازه های کوچکتر و فاصله فشرده تر است که باعث می شود یک کوچک شدن ساده برای کاهش هزینه ها و بهبود عملکرد [5] تا حدی به دلیل افزایش تراکم ترانزیستور (تعداد ترانزیستور در هر میلی متر مربع) نیاز باشد. فرآیندهای نیمرسانا اولیه دارای نام های دلخواه بود، نام هایی مانند HMOS III ، CHMOS V ؛ موارد بعدی با اندازه مانند فرایند 90 نانومتر ذکر می شوند .
طبق استاندارد صنعت ، هر نسل از فرآیند تولید نیمرسانا ، که به عنوان گره فناوری یا گره فرآیند نیز شناخته می شود ، [6] با حداقل اندازهٔ مشخصه فرآیند تعیین می شود. گره های فناوری ، همچنین به عنوان "فن آوری های فرآیند" یا به سادگی "گره ها" شناخته می شوند ، به طور معمول با اندازه در نانومتر (یا به لحاظ تاریخی میکرومتر ) طول دروازه ترانزیستور فرآیند نشان داده می شوند. با این حال ، از سال 1994 تاکنون چنین نبوده است. در ابتدا طول دروازه ترانزیستور کوچکتر از نام پیشنهاد شدهی گره فرآیند بود (به عنوان مثال گره 350nm ) ؛ با این حال این روند در سال 2009 معکوس شد. [7] نانومتری که برای نامگذاری گره های فرایند استفاده می شود بیشتر به اصطلاح بازاریابی تبدیل شده است که هیچ ارتباطی با اندازه واقعی ویژگی و تراکم ترانزیستور ندارد (تعداد ترانزیستور در میلی متر مربع). به عنوان مثال ، پردازش 10nm اینتل، در واقع دارای ویژگی هایی (نوک باله های FinFET) با عرض 7nm است ، پردازش اینتلِ 10nm از نظر تراکم ترانزیستور مشابه TSMC 7nm است ، در حالی که پردازش GlobalFoundries 12nm و 14nm دارای اندازهٔ مشخصه های مشابه هستند. [8] [9] [10]
لیست مراحل
این لیستی از تکنیک های پردازش است که چندین بار در طول ساخت یک دستگاه الکترونیکی مدرن استفاده می شود. این لیست لزوماً به معنی نظم خاصی نیست. تجهیزات انجام این فرآیندها توسط تعداد معدودی از شرکت ها ساخته شده است. قبل از شروع کار، کلیه تجهیزات باید آزمایش شوند. [11]
- فرآوری ویفر
- تمیز کردن مرطوب
- تمیز کردن توسط حلالهایی مانند استون ، تری کلرواتیلن و آب فوق العاده خالص
- محلول پیرانا
- RCA تمیز
- غیرفعال سازی سطح
- فوتولیتوگرافی
- کاشت یون (که در آن دوپانت در ویفر جاسازی می شود و مناطقی را با افزایش یا کاهش رسانایی ایجاد می کند)
- اچینگ (میکروپارچینگ)
- اچینگ خشک ( اچ پلاسما )
- اچینگ یون غیرفعال (RIE)
- اچینگ عمیق یون غیرفعال
- اچینگ لایه اتمی (ALE)
- اچینگ یون غیرفعال (RIE)
- اچینگ مرطوب
- اچینگ اکسید بافر شده
- اچینگ خشک ( اچ پلاسما )
- خاکستر شدن پلاسما
- فرایندهای حرارتی
- آنیل حرارتی سریع
- آنیل کوره ای
- اکسیداسیون حرارتی
- رسوب بخار شیمیایی (CVD)
- رسوب لایه اتمی (ALD)
- رسوب بخار فیزیکی (PVD)
- برآرایی پرتو مولکولی (MBE)
- لیزر لیفت (برای تولید LED [12] )
- رسوب الکتروشیمیایی (ECD). رجوع کنید به آبکاری
- مسطح سازی شیمیایی - مکانیکی (CMP)
- تست ویفر (جایی که عملکرد الکتریکی با استفاده از تجهیزات آزمایش خودکار تأیید میشود، پیرایش لیزر نیز در این مرحله ممکن است انجام شود)
- تمیز کردن مرطوب
- آماده سازی ریخته گری
- ساخت و تولید میانراه سیلیکونی (برای مدارهای مجتمع سه بعدی )
- نصب ویفر (ویفر با استفاده از نوار برشزنی روی یک قاب فلزی نصب می شود)
- خرد کردن و مسطح سازی [13] (ضخامت ویفر را برای دستگاه های نازک مانند کارت هوشمند یا کارت PCMCIA یا اتصال ویفر و یا بسته شدن ویفر کاهش می دهد ، این امر همچنین می تواند در هنگام قیمت گذاری ویفر اتفاق بیفتد ، در فرآیندی که به عنوان Dice Before Grind یا DBG شناخته می شود [14] [15] )
- اتصال و انباشت ویفر (برای مدارهای مجتمع سه بعدی و MEMS )
- ساخت و تولید لایه توزیع مجدد (برای بسته های WLCSP)
- بستن ویفر (برای تراشه واگرد BGA ( آرایه شبکه توپی ) و بسته های WLCSP)
- برش دای یا تکه ویفر
- بسته بندی IC
- ضمیمه دای (دای با استفاده از خمیر رسانا یا فیلم ضمیمه دای به یک قاب سرب متصل می شود [16] [17] )
- اتصال IC: اتصال سیم ، اتصال حرارتی ، تراشه واگرد یا اتصال خودکار نوار (TAB)
- نصب کپسول سازی IC یا پخش کننده حرارت یکپارچه (IHS)
- قالب گیری (با استفاده از ترکیب خاص قالب گیری که ممکن است حاوی پودر شیشه به عنوان پرکننده باشد)
- پخت
- آبکاری الکترولیتی (صفحات سر مس قاب های سربی با قلع برای سهولت کار لحیم کاری)
- علامت گذاری با لیزر یا چاپ روی صفحه
- اصلاح و شکل دادن (قابهای سرب را از یکدیگر جدا می کند ، و پایه های قاب سر را خم می کند تا بتوان آنها را بر روی یک صفحه مدار چاپی نصب کرد)
- تست آی سی
- فرآوری ویفر
بعلاوه ممکن است مراحلی مانند رایت اچینگ نیز انجام شود.
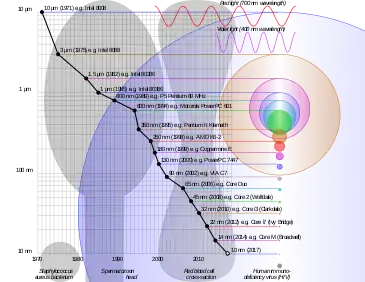
جلوگیری از آلودگی و نقص
وقتی عرض مشخصه ها به مراتب بیشتر از 10 میکرومتر بود، خلوص نیمرساناها به اندازه امروز در ساخت و تولید دستگاه مسئله ای نبود. با ادغام بیشتر دستگاه ها ، اتاق های تمیز باید حتی تمیزتر شوند. امروزه کارخانه های تولیدی با هوای فیلتر شده تحت فشار قرار می گیرند تا حتی کوچکترین ذرات از بین بروند که ممکن است روی ویفرها بنشینند و به نقص کمک کنند. سقف اتاق های تمیز نیمرساناها دارای واحدهای فیلتر فن (FFU) در فواصل منظم هستند تا دائماً فضای اتاق تمیز را تعویض و فیلتر کنند. تجهیزات سرمایه نیمرساناها نیز ممکن است FFU خاص خود را داشته باشند. FFU ها ، همراه با کف های بلند شده با کوره ها ، به اطمینان از جریان هوای چند لایه کمک می کنند تا اطمینان حاصل شود که ذرات بلافاصله به پایین بر روی کف آورده می شوند و به دلیل تلاطم در هوا معلق نمی مانند. کارگران در یک مرکز ساخت نیم رسانا ملزم به پوشیدن لباس تمیز برای محافظت از دستگاهها در برابر آلودگی انسان هستند. برای جلوگیری از اکسید شدن و افزایش عملکرد ، FOUP ها و تجهیزات سرمایهای نیمرسانا ممکن است دارای یک محیط نیتروژن خالص مهر و موم شده با سطح گرد و غبار کلاس ISO 1 باشند. FOUPs و غلافهای SMIF ویفرها را از فضای اتاق تمیز جدا کرده و عملکرد را افزایش می دهند زیرا تعداد نقص های ناشی از ذرات گرد و غبار را کاهش می دهند. همچنین ، Fabs تا آنجا که ممکن است تعداد افراد کمتری در اتاق تمیز نگه میدارند تا حفظ محیط اتاق تمیز را آسان تر کند ، از آنجا که افراد ، حتی هنگامی که لباس تمیز پوشیدهاند ، مقادیر زیادی ذرات به خصوص هنگام راه رفتن، دارند. [18] [19] [20]
ویفرها
یک ویفر معمولی از سیلیکون کاملاً خالص ساخته می شود که با استفاده از فرایند چکرالسکی به صورت شمش استوانه ای تک بلوری ( بول ) تا قطر 300 میلیمتر(کمی کمتر از 12 اینچ) رشد میکند. سپس این شمش ها در ضخامت حدود 0.75 میلیمتر به صورت ویفرهای برش خورده در می آیند و برای بدست آوردن یک سطح کاملا منظم و صاف صیقلی میشوند.
فرآیند ساخت
در ساخت دستگاه های نیمرسانا ، مراحل مختلف فرآوری در چهار دسته کلی قرار می گیرد: رسوب گذاری ، حذف ، الگوسازی و اصلاح خصوصیات الکتریکی.
- رسوب گذاری به هر روشی گفته می شود که رشد ، پوشاندن یا انتقال مواد دیگر به ویفر انجام شود. فن آوری های موجود شامل رسوب بخار فیزیکی (PVD) ، رسوب بخار شیمیایی (CVD) ، رسوب الکتروشیمیایی (ECD) ، برآرایی پرتو-مولکولی (MBE) ، و اخیراً ، رسوب لایه اتمی (ALD) در میان سایر موارد است. رسوب را می توان شامل تشکیل لایه اکسید،، توسط اکسیداسیون حرارتی یا به طور خاص تر ، LOCOS دانست .
- حذف، هر فرآیندی است که مواد را از ویفر خارج می کند. مثالها شامل فرآیندهای اچینگ ( مرطوب یا خشک ) و مسطح سازی شیمیایی - مکانیکی (CMP) است.
- الگو سازی، شکل دادن یا تغییر دادن مواد رسوب شده است و به طور کلی لیتوگرافی نامیده می شود. به عنوان مثال ، در لیتوگرافی مرسوم ، ویفر با ماده شیمیایی به نام لاک نوری پوشانده می شود. سپس ، دستگاهی موسوم به استپر ، با تمرکز ، تراز و حرکت یک ماسک ، قسمتهای مختلف ویفر را در معرض نور طول موج کوتاه قرار می دهد. مناطق در معرض توسط یک محلول توسعه دهنده شسته می شوند. پس از اچ یا پردازش دیگر ، مقاومت در برابر نور با استفاده از خاکستر پلاسمای "خشک" (سلب یا نوار مقاومت در برابر نور) برداشته می شود. همچنین ممکن است مقاومت در برابر نور با استفاده از فرآیندهای شیمیایی مرطوب که ویفر را در یک مایع می پوشاند ، حذف شود تا مقاومت در برابر نور از بین برود. [21]
- اصلاح خصوصیات الکتریکی به صورت تاریخی شامل آلایش و تخلیه منابع ترانزیستور (در اصل توسط کوره های انتشار و بعداً با کاشت یون ) می شود. این فرآیند های آلایش با آنیل کوره یا در دستگاه های پیشرفته با آنیل حرارتی سریع (RTA) دنبال می شود. آنیل برای فعال کردن دوپانتهای کاشته شده عمل می کند. اکنون اصلاح خصوصیات الکتریکی شامل کاهش ثابت دی الکتریک ماده در دیالکتریک با کاپای کم از طریق قرار گرفتن در معرض نور فرابنفش در فرآیند UV (UVP) نیز میشود. اصلاح غالباً توسط اکسیداسیون حاصل می شود ، که می تواند برای ایجاد اتصالات عایق نیمرسانا ، مانند اکسیداسیون محلی سیلیکون ( LOCOS ) برای ساخت ماسفت ، انجام شود .
تراشه های مدرن حداکثر تا یازده سطح فلز یا بیشتر در بیش از 300 مرحله فرآوری ترتیبی تولید میشوند.
فرایند Front-end-of-line (FEOL)
فرایند FEOL به تشکیل ترانزیستورها به طور مستقیم در سیلیکون اشاره دارد. ویفر خام با رشد یک لایه سیلیکون کاملاً خالص و بدون نقص از طریق برآرایی مهندسی می شود. در پیشرفته ترین دروازه های منطقی ، قبل از مرحله برآرایی سیلیکون ، ترفندهایی برای بهبود عملکرد ترانزیستورهای ساخته شده انجام می شود. یک روش شامل معرفی مرحله صافی است که در آن یک نوع سیلیکون مانند سیلیکون-ژرمانیم (SiGe) رسوب می کند. پس از رسوب سیلیکون برآرایی شده ، شبکه کریستال تا حدودی کشیده می شود و در نتیجه باعث بهبود تحرک الکترونیکی می شود. روش دیگری به نام فناوری سیلیکون بر روی عایق شامل قرار دادن یک لایه عایق بین ویفر سیلیکون خام و لایه نازک برآرایی شده سیلیکون بعدی است. این روش منجر به ایجاد ترانزیستور با اثرات پراکند کاهش یافته می شود.
اکسید گیت و کاشت
مهندسی سطح Front-end با رشد دی الکتریک گیت (به طور سنتی دی اکسید سیلیکون ) ، الگوسازی دروازه ، الگوسازی مناطق منبع و تخلیه و کاشت یا انتشار بعدی مخازن برای بدست آوردن خصوصیات الکتریکی مکمل به دنبال دارد. در دستگاه های حافظه تصادفی پویا (DRAM) ، خازن های ذخیره سازی نیز در این زمان ساخته می شوند ، که به طور معمول بالای ترانزیستور دسترسی قرار می گیرند (سازنده DRAM که اکنون از کار افتاده است ، Qimonda این خازن ها را با سنگرهایی که در عمق سطح سیلیکون قرار دارند ، اجرا کرد)
لایه های فلزی
پس از ایجاد وسایل نیمرسانا مختلف ، باید آنها را بهم متصل کرد تا مدارهای الکتریکی مورد نظر را تشکیل دهند. این در یک سری از مراحل فرآوری ویفر در مجموع به عنوان BEOL رخ می دهد ( با پایان دادن به عقب ساخت تراشه، که با اشاره به بسته بندی و مراحل آزمایش اشتباه گرفته نشود). فرایند BEOL شامل ایجاد سیمهای متصل به فلز است که توسط لایه های دی الکتریک جدا شده اند. ماده عایق به طور سنتی یک شکل از SiO2 یا یک شیشه سیلیکاتی است ، اما به تازگی مواد جدید دی الکتریک با کاپای کم استفاده می شود (مانند oxycarbide سیلیکون)، به طور معمول ثابت دی الکتریک در حدود 2.7 است (در مقایسه با 3.82 برای SiO2) ، اگر چه مواد با ثابت های کم 2.2 ، به تولیدکنندگان ارائه می شود. در عوض ممکن است از دی الکتریک با کاپای زیاد استفاده شود.
میانهابندها
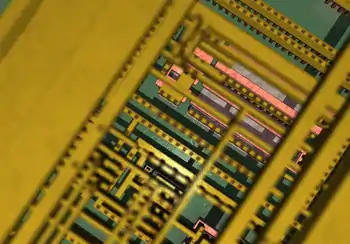
از لحاظ تاریخی ، سیمهای فلزی از آلومینیوم تشکیل شده اند. در این رویکرد سیم کشی (که اغلب آلومینیوم کم کننده نامیده می شود) ، ابتدا فیلمهای خالی آلومینیوم رسوب داده می شوند ، الگو می گیرند و سپس اچ می شوند و سیمهای جدا شده باقی می مانند. سپس مواد دی الکتریک بر روی سیمهای در معرض رسوب قرار می گیرد. لایه های مختلف فلزی توسط اچینگ سوراخ ها (به نام " ویاس") در مواد عایق به یکدیگر متصل می شوند و سپس با استفاده از روش CVD با استفاده از هگزا فلورید تنگستن ، تنگستن را در آنها قرار می دهند. این روش هنوز هم در ساخت بسیاری از تراشه های حافظه مانند حافظه تصادفی پویا (DRAM) استفاده می شود ، زیرا تعداد سطوح اتصال کم است (در حال حاضر بیش از چهار مورد نیست).
اخیراً ، با توجه به تعداد ترانزیستورهایی که اکنون در یک ریزپردازنده مدرن به هم متصل شده اند ، میزان سطح اتصال برای منطق کامپیوتری به میزان قابل توجهی افزایش یافته است ، تاخیر زمان بندی سیم کشی به قدری قابل توجه شده است که باعث تغییر در مواد سیم کشی می شود (از آلومینیوم به لایه اتصال مس) و تغییر در مواد دی الکتریک (از دی اکسیدهای سیلیسیم به دی الکتریک با کاپای کم ). این افزایش عملکرد همچنین از طریق فرایند داماسن با کاهش هزینه همراه است که مراحل فرآوری را از بین می برد. با افزایش تعداد سطوح اتصال ، برای اطمینان از یک سطح صاف قبل از لیتوگرافی بعدی ، به مسطح سازی لایه های قبلی نیاز است. بدون آن ، سطوح به طور فزاینده ای کج می شوند ، و از عمق تمرکز لیتوگرافی موجود گسترش می یابند ، و بنابراین در توانایی الگو سازی تداخل ایجاد می کنند. CMP ( مسطح سازی شیمیایی-مکانیکی ) روش اصلی پردازش برای دستیابی به چنین مسطحسازی ای است ، اگرچه اگر تعداد سطح اتصال بیش از سه نباشد ، اچ خشک هنوز هم استفاده می شود. اتصالات مس از یک لایه سد رسانای الکتریکی استفاده می کنند تا از انتشار مس در محیط اطراف خود ("مسمومیت") جلوگیری کند.
تست ویفر
ماهیت کاملاً سریالی فرآوری ویفر ، تقاضا برای مترولوژی را در بین مراحل مختلف فرایند افزایش داده است. به عنوان مثال ، از مترولوژی فیلم نازک مبتنی بر بیضی سنجی یا انعکاس سنجی برای کنترل دقیق ضخامت اکسید دروازه ، همچنین ضخامت ، ضریب شکست و ضریب انقراض پوشش های مقاوم در برابر نور و سایر پوشش ها استفاده می شود. تجهیزات اندازه گیری تست ویفر برای اطمینان از آسیب ندیدن ویفرها توسط مراحل فرایند قبلی تا آزمایش استفاده می شود. اگر بیش از حد بسیاری از دای ها در یک ویفر شکست بخورند، کل ویفر اوراق است تا از هزینه های فرآوری بیشتر جلوگیری شود. از مترولوژی مجازی برای پیش بینی خواص ویفر بر اساس روش های آماری بدون انجام اندازه گیری فیزیکی استفاده شده است. [22]
تست دستگاه
پس از اتمام مراحل front-end ، دستگاه های نیمرسانا یا تراشه ها، تحت آزمایش های الکتریکی مختلفی قرار می گیرند تا مشخص شود که آیا آنها به درستی کار می کنند یا خیر. درصد دستگاههای موجود در ویفر که عملکرد مناسبی دارند به عنوان بازده نامیده می شود. تولیدکنندگان معمولاً در مورد عملکرد خود پنهانی عمل می کنند ، اما ممکن است به 30٪ هم برسد ، به این معنی که فقط 30٪ از تراشه های ویفر مطابق آنچه در نظر گرفته شده کار می کنند. تنوع فرآیند یکی از دلایل عملکرد کم است. آزمایش برای جلوگیری از مونتاژ تراشه ها در بسته های نسبتاً گران انجام می شود.
عملکرد اغلب (نه لزوما) مربوط به اندازه دستگاه (دای یا تراشه) است. به عنوان مثال ، در دسامبر 2019 ، TSMC عملکرد متوسط 80% را با حداکثر عملکرد 90% را در هر ویفر برای تراشه های آزمایش 5 نانومتری خود با اندازه دای 17.92 میلی مترمربع اعلام کرد. عملکرد با افزایش اندازه دای به 100.0 میلی مترمربع به 32.0٪ کاهش یافت. [23]
Fab با تراشه الکترونیکی تراشه های ویفر را آزمایش می کند که کاوشگرهای ریز را بر روی تراشه فشار می دهد. دستگاه هر قطعه بد را با یک قطره رنگ علامت گذاری می کند. در حال حاضر ، اگر داده های آزمایش ویفر (نتایج) در یک بانک اطلاعاتی رایانه مرکزی وارد شوند و تراشه ها مطابق با محدودیت های آزمایشی از پیش تعیین شده مانند حداکثر فرکانس ها / ساعتها ، تعداد هسته های فعال در هر تراشه (کاملاً کاربردی)وغیره ، "تصفیه" شوند (یعنی مرتب سازی در سطل های مجازی)، علامت گذاری رنگ الکترونیکی امکان پذیر است. داده های تصیفیهشده حاصل را می توان روی نقشه ویفر پیکربندی یا ثبت کرد تا نقص تولید را ردیابی کند و تراشه های بد را علامت گذاری کند. از این نقشه می توان در هنگام جمع آوری و بسته بندی ویفر نیز استفاده کرد. تصفیهکردن اجازه می دهد تا تراشه هایی که در غیر این صورت رد می شوند ، در محصولات سطح پایین مورد استفاده مجدد قرار گیرند ، همانطور که در مورد پردازنده های گرافیکی و پردازنده ها وجود دارد ، عملکرد دستگاه را افزایش می دهد ، به خصوص اینکه تراشه های بسیار کمی کاملاً کاربردی هستند (به عنوان مثال همه هسته ها به درستی کار می کنند).از eFUSE ها ممکن است برای جدا کردن قسمتهایی از تراشه ها مانند هسته استفاده شود ، زیرا به این دلیل که در هنگام تصفیهکردن کار نکرده اند یا به عنوان بخشی از تقسیم بازار (با استفاده از همان تراشه برای سطوح پایین ، متوسط و سطح بالا). تراشه ها ممکن است قطعات یدکی داشته باشند تا تراشه بتواند آزمایش خود را به طور کامل پشت سر بگذارد حتی اگر دارای چندین قسمت غیر کار باشد.
تراشه ها نیز پس از بسته بندی مجدداً آزمایش می شوند ، زیرا ممکن است سیمهای اتصال از بین رفته باشند یا عملکرد آنالوگ توسط بسته تغییر کند. از این به عنوان "آزمون نهایی" یاد می شود. همچنین ممکن است از تراشه ها با استفاده از اشعه ایکس تصویربرداری شود.
معمولاً Fab برای زمان آزمایش هزینه دارد و قیمت آن در حدود سنت در ثانیه است. زمان آزمایش از چند میلی ثانیه تا چند ثانیه متفاوت است و نرم افزار آزمون برای کاهش زمان تست بهینه شده است. آزمایش تراشه های چندگانه (چند سایته) نیز ممکن است زیرا بسیاری از آزمایش کنندگان منابعی را دارند که می توانند بیشتر یا همه آزمایشات را به صورت موازی و همزمان روی چندین تراشه انجام دهند.
تراشه ها اغلب با "ویژگی های آزمایش پذیری" مانند زنجیره های اسکن یا " خودآزمایی داخلی " برای آزمایش سریع و کاهش هزینه های آزمایش طراحی می شوند. در برخی از طرح ها که از فرایندهای ویژه آنالوگ Fab استفاده می کنند ، ویفرها نیز در حین آزمایش با لیزر اصلاح می شوند تا مقادیر مقاومت کاملاً توزیع شده ای که توسط طرح مشخص شده است ، حاصل شود.
طراحی های خوب سعی در تست و مدیریت آماری گوشه ها (شدت رفتار سیلیکون ناشی از دمای عملیاتی بالا همراه با مراحل فرآوری Fab) دارند. اکثر طرح ها حداقل با 64 گوشه کنار می آیند.
عملکرد دستگاه
بازده دستگاه یا بازده دای ، تعداد تراشه های در حال کار یا دای روی ویفر است که به درصد داده می شود زیرا تعداد تراشه های ویفر (Die per wafer، DPW) بسته به اندازه تراشه ها و قطر ویفر متفاوت است. تخریب عملکرد کاهش عملکرد است که در طول تاریخ عمدتا توسط ذرات گرد و غبار ایجاد می شد ، با این حال از دهه 1990 ، تخریب عملکرد عمدتا به دلیل تغییر فرایند ، خود فرایند و توسط ابزارهای مورد استفاده در تولید تراشه ایجاد می شود ، اگرچه گرد و غبار هنوز به عنوان یک مشکل در بسیاری از Fab های قدیمی باقی مانده است. ذرات گرد و غبار اثر فزاینده ای بر عملکرد دارند زیرا اندازه مشخصه ها با فرآیندهای جدید کاهش می یابد. اتوماسیون و استفاده از محیط های کوچک در داخل تجهیزات تولید ، FOUPs و SMIF ها امکان کاهش نقص ناشی از ذرات گرد و غبار را فراهم کرده است. بازده دستگاه باید بالا باشد تا قیمت فروش تراشه های در حال کار کاهش یابد زیرا تراشه های در حال کار باید هزینه آن تراشه های خراب را پرداخت کنند و هزینه فرآوری ویفر را کاهش دهند. عملکرد و تولید نیز می تواند تحت تأثیر طراحی و عملکرد Fab باشد.
کنترل دقیق آلاینده ها و فرآیند تولید برای افزایش عملکرد لازم است. آلاینده ها ممکن است آلاینده های شیمیایی یا ذرات گرد و غبار باشند. "نقص های کشنده" مواردی است که توسط ذرات گرد و غبار ایجاد می شود که باعث خرابی کامل دستگاه می شود (مانند ترانزیستور). نقص های بی ضرری نیز وجود دارد. یک ذره باید به اندازه 1/5 یک ویژگی باشد تا نقص قاتل ایجاد کند. بنابراین اگر یک ویژگی 100nm باشد ، یه ذره برای ایجاد نقص قاتل فقط باید 20nm باشد. برق الکترواستاتیک نیز می تواند بر عملکرد تأثیر منفی بگذارد. آلاینده های شیمیایی یا ناخالصی ها شامل فلزات سنگین مانند آهن ، مس ، نیکل ، روی ، کروم ، طلا ، جیوه و نقره ، فلزات قلیایی مانند سدیم ، پتاسیم و لیتیوم و عناصری مانند آلومینیوم ، منیزیم ، کلسیم ، کلر ، گوگرد ، کربن، و فلوئور است . برای آن عناصر مهم است که با سیلیکون در تماس نباشند ، زیرا می توانند عملکرد را کاهش دهند. از مخلوط های شیمیایی می توان برای حذف این عناصر از سیلیکون استفاده کرد. مخلوط های مختلف در برابر عناصر مختلف موثر هستند.
چندین مدل برای تخمین عملکرد استفاده می شود. آنها مدل مورفی ، مدل پواسون ، مدل دوجمله ای ، مدل مور و مدل دانه ها هستند. هیچ مدل جهانی وجود ندارد. یک مدل باید براساس توزیع عملکرد واقعی (محل تراشه های معیوب) انتخاب شود. به عنوان مثال ، مدل مورفی فرض می کند که افت عملکرد بیشتر در لبه های ویفر اتفاق می افتد (تراشه های غیرفعال در لبه های ویفر متمرکز شده اند) ، مدل پواسون فرض می کند که دای های معیوب به طور مساوی در ویفر پخش می شوند و مدل دانه ها فرض می کند که دای های معیوب بهم پیوسته اند. [24]
هزینه تولید دایهای كوچكتر كمتر است (از آنجا كه بیشتر برای ویفر مناسب است و ویفرها به طور كلی فرآوری و قیمت گذاری می شوند)، و می تواند به دستیابی به بازده بالاتر كمك كند ، زیرا دایهای كوچكتر دارای شانس كمتری برای نقص هستند ، زیرا سطح پایین آنها روی ویفر بیشتر است. با این حال ، دای های کوچکتر برای دستیابی به عملکردهای مشابه دای های بزرگتر یا پیشی گرفتن از آنها ، به ویژگی های کوچکتر نیاز دارند و ویژگی های کوچکتر نیز برای حفظ بازده بالا به تغییر روند و کاهش خلوص (کاهش آلودگی) نیاز دارند. از ابزارهای مترولوژی برای بازرسی ویفرها در طول فرآیند تولید و پیش بینی عملکرد استفاده می شود ، بنابراین ویفرهایی که پیش بینی می شود نقص زیادی داشته باشند ممکن است برای صرفه جویی در هزینه های فرآوری ، از بین بروند. [25]
آماده سازی دای
پس از آزمایش ، ویفر معمولاً در فرایندی که به عنوان "backlap" [26]، "backfinish" یا "رقیق شدن ویفر" [27] نیز شناخته می شود ، قبل از امتیاز دهی ویفر و سپس خرد شدن ویفر ، از ضخامت آن کاسته می شود ، که این فرآیند به ویفر قیمتی معروف است.فقط تراشه های خوب و بدون علامت بسته بندی می شوند.
بسته بندی
بسته بندی پلاستیکی یا سرامیکی شامل نصب دای ، اتصال لنت های دای به سنجاق های بسته بندی و آب بندی دای است. از سیمهای اتصال ریز برای اتصال لنت ها به پایه ها استفاده می شود. در روزگار قدیم ، سیمها با دست متصل می شدند ، اما اکنون ماشین آلات تخصصی وظیفه را انجام می دهند. به طور سنتی ، این سیمها از طلا تشکیل شده اند ، که منجر به یک قاب سربی (تلفظ "قاب چوبی") از مس روکش شده لحیم می شود. سرب سمی است ، بنابراین "قابهای سربی" بدون سرب اکنون توسط RoHS مجاز شده اند.
بسته مقیاس تراشه (CSP) یکی دیگر از فناوری های بسته بندی است. یک بسته پلاستیکی دی آی پی ، مانند اکثر بسته ها ، چندین برابر بزرگتر از دای واقعی مخفی شده در داخل است ، در حالی که تراشه های CSP تقریباً به اندازه دای هستند. قبل از اینکه ویفر خرد شود ، می توان CSP برای هر دای ساخت.
تراشه های بسته بندی شده مجدداً آزمایش می شوند تا اطمینان حاصل کنند که در حین بسته بندی صدمه ای ندیده اند و عملیات اتصال اتصالات دای به پین به درستی انجام شده است. سپس یک لیزر نام تراشه و اعداد را روی بسته بندی حک می کند.
مواد خطرناک
در فرآیند ساخت از بسیاری از مواد سمی استفاده می شود. [28] این شامل:
- عناصر سمی آلاینده ، مانند آرسنیک ، آنتیموان و فسفر .
- ترکیبات سمی ، مانند آرسین ، فسفین ، هگزا فلورید تنگستن و سیلان .
- مایعات بسیار واکنش پذیر ، مانند پراکسید هیدروژن ، بخور اسید نیتریک ، اسید سولفوریک و اسید هیدروفلوئوریک .
بسیار مهم است که کارگران نباید مستقیماً در معرض این مواد خطرناک قرار بگیرند. درجه بالای اتوماسیون رایج در صنعت ساخت IC باعث کاهش احتمال قرار گرفتن در معرض خطر میشود. در بیشتر تأسیسات ساختمانی از سیستم های مدیریت اگزوز مانند اسکرابر مرطوب ، احتراق ، کارتریج جاذب گرم شده و غیره استفاده می شود تا خطر کارگران و محیط را کنترل کند.
جستار های وابسته
- ایست نقصی
- لیست نمونه های مقیاس نیمرسانا
- ماسفت
- قطعه چندگیتی
- صنایع نیمرسانا
- مدل ریخته گری
- تلفیق نیمرسانا
- لوکاس ( LOCOS )
- ریزساخت
- عدد ترانزیستور
- غیرفعالسازی
- فرایند مسطح
منابع
- Neurotechnology Group, Berlin Institute of Technology, IEEE Xplore Digital Library. “Regression Methods for Virtual Metrology of Layer Thickness in Chemical Vapor Deposition.” January 17, 2014. Retrieved November 9, 2015.
- "8 Things You Should Know About Water & Semiconductors". ChinaWaterRisk.org. Retrieved 2017-09-10.
- Kure, T.; Hanaoka, Hideo; Sugiura, T.; Nakagawa, S. (October 23, 2007). "Clean-room Technologies for the Mini-environment Age".
- "FOUP Purge System - Fabmatics: Semiconductor Manufacturing Automation". www.fabmatics.com.
- Ken Shirriff. "Die shrink: How Intel scaled-down the 8086 processor". 2020.
- https://en.wikichip.org/wiki/technology_node#:~:text=The%20technology%20node%20(also%20process,process%20and%20its%20design%20rules.&text=Generally%2C%20the%20smaller%20the%20technology,faster%20and%20more%20power-efficient.
- "Full Page Reload". IEEE Spectrum: Technology, Engineering, and Science News.
- Cutress, Ian. "Intel's 10nm Cannon Lake and Core i3-8121U Deep Dive Review". www.anandtech.com.
- https://fuse.wikichip.org/news/1497/vlsi-2018-globalfoundries-12nm-leading-performance-12lp/
- Ridley, Jacob (April 29, 2020). "Intel 10nm isn't bigger than AMD 7nm, you're just measuring wrong".
- "Power outage partially halts Toshiba Memory's chip plant". Reuters. June 21, 2019.
- "Laser Lift-Off(LLO) Ideal for high brightness vertical LED manufacturing - Press Release - DISCO Corporation". www.disco.co.jp.
- "Product Information | Polishers - DISCO Corporation". www.disco.co.jp.
- "Product Information | DBG / Package Singulation - DISCO Corporation". www.disco.co.jp.
- "Plasma Dicing (Dice Before Grind) | Orbotech". www.orbotech.com.
- "Electro Conductive Die Attach Film(Under Development) | Nitto". www.nitto.com. Archived from the original on 26 May 2019. Retrieved 13 July 2020.
- "Die Attach Film Adhesives". www.henkel-adhesives.com.
- "The ASYST SMIF system - Integrated with the Tencor Surfscan 7200". Chip History.
- "Study into human particle shedding". www.cleanroomtechnology.com.
- "How a Chip Gets Made: Visiting GlobalFoundries". PCMag Asia. February 15, 2018.
- "Wafer Cleaning Procedures; Photoresist or Resist Stripping; Removal of Films and Particulates". www.eesemi.com.
- Neurotechnology Group, Berlin Institute of Technology, IEEE Xplore Digital Library. “Regression Methods for Virtual Metrology of Layer Thickness in Chemical Vapor Deposition.” January 17, 2014. Retrieved November 9, 2015.
- Cutress, Dr Ian. "Early TSMC 5nm Test Chip Yields 80%, HVM Coming in H1 2020". www.anandtech.com.
- https://dokumente.unibw.de/pub/bscw.cgi/d10465215/%C3%9Cbung-1.pdf
- http://smithsonianchips.si.edu/ice/cd/CEICM/SECTION3.pdf
- "Introduction to Semiconductor Technology" (PDF). STMicroelectronics. p. 6.
- "Wafer Backgrind". eesemi.com.
- CNET. “Why tech pollution's going global.” April 25, 2002. Retrieved November 9, 2015.
مطالعه بیشتر
- Kaeslin, Hubert (2008), Digital Integrated Circuit Design, from VLSI Architectures to CMOS Fabrication, Cambridge University Press, section 14.2.
- Wiki related to Chip Technology