سختکاری سطحی با لیزر
سخت کردن سطحی قطعات توسط پرتو لیزر،(به انگلیسی:Laser-hardening ) با فرایندهای دیگر سخت کردن سطحی تفاوت اساسی ندارد . بطور کلی در تمام این روش ها ، سخت کاری سطحی با سرد کردن سریع قطعه فولادی از دمای استنبتی صورت می گیرد.
با توجه به اینکه سرعت انتقال حرارت در مصالح فولادی نسبتاً زیاد است، لذا استفاده از منبعی با قدرت حرارتی و گرمادهی ویژه بالا ، برای گرم کردن سریع قطعه ، ضروری میباشد. سخت کردن سطح قطعات فولادی از قبیل چرخ دنده ها ، قالب ها و ابزار دقیق توسط اشعه لیزر در سالهای اخیر توسعه یافته است.
توسط اشعه لیزر می توان یک جریان بسیار شدید انرژی را در موضع کوچکی از سطح قطعه متمرکز کرد. در این حالت، پروفیل حرارت ، از سطح به طرف مرکز قطعه ، شیب تندی دارد. در نتیجه در این روش ، نیازی به محیط سردکننده خارجی نمیباشد.
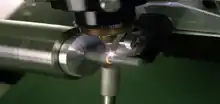
تاریخچه
در سال ۱۹۹۷ اینشتین واقعیتی را بیان کرد که از لحاظ تکنولوژی دارای اهمیت زیادی است. اینشتین نشان داد در صورتی که یک اتم تحریک شده، پیش از رسیدن به سطح پایین انرژی، با یک فوتونی با همان انرژی برخورد کند، دو فوتون انرژی، که شامل فوتون اولیه و فوتون تحریک شده است ، حاصل میشود. این دو فوتون که هر دو دارای سطح انرژی یکسان خواهند بود، در عین حال دارای یک جهت و دقیقاً باهم در یک فاز هستند. این نظریه پایه و اساس روش تقویت نور و سپس تولید انواع پرتو لیزر قرار گرفت.
ویژگی لیزر
پرتو لیزر نوری است که اساساً مستقل از شکل و ویژگی های قطعه عمل کرده ، بدون نیاز به خط برده ، به آسانی کنترل می شود و نیز محصول احتراق ندارد. واگرایی اشعه لیزر بسیار کم میباشد، بطوری که اگر پرتو باریکی از آن ، از سطح زمین بر روی سطح ماه تابانده شود، فقط منطقه ای به قطر حدود سه کیلومتر را روشن می سازد. دو ویژگی مهم دیگر اشعه لیزر آنست که :
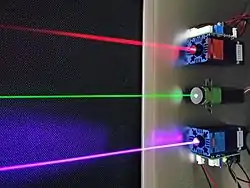
- اولا تمام نورهای موجود در آن دارای یک طول موج بوده،
- ثانیاً همه نورها نسبت به هم در یک فاز هستند.
فرایند
فرایند های سخت کردن سطحی در کل (به جز نفوذ کربن یا نیتروژن[1]) بر پایه ی بالا بردن دمای سطح فلز تا محدوده ی آستنیتی و سرد کردن سریع فولاد تا فاز سخت و با استحکام بالای مارتنزیت استکه گاهی با یک عملیات حرارتی بسیار کم دما به منظور ایجاد کیفیت سطحی بالاتر و کاستن از تردی پیگیری می شود. حال این بالا بردن دما و کوئنچ می تواند با شعله ی آتش و آب، القای الکترو مغناطیس و آب(یا روغن) و یا اشعه لیزر و هوا با شد. هر کدام از این موارد ویژگی هایی دارند که در جدول زیر می آید:[2]
سختکاری با شعله | سختکاری القایی | سختکاری با لیزر | |
---|---|---|---|
عمق | کم و زیاد | کم و زیاد | کم |
منطقه موثر | بزرگ | متوسط | بسیار کوچک |
دقت | کم | متوسط | زیاد |
کنترل پذیری فرایند | کم | زیاد | متوسط |
اصول سخت کردن سطح قطعه با پرتو لیزر
پرتو لیزر به عنوان یک منبع حرارتی می تواند برای سخت کاری سطحی قطعه و یا ایجاد یک لایه مذاب یکنواخت ، از تقریباً همه آلیاژها ، بر روی سطح جسم، مورد استفاده قرار گیرد. وقتی دسته پرتوی با قدرت نسبتاً بالا بر روی سطح فولاد تابانیده شود، سطح قطعه، با سرعتی خیلی بیشتر از سرعت انتقال حرارت به داخل آن، گرم می شود. به این ترتیب، در حالیکه قسمت داخلی قطعه هنوز سرد است ، یک لایه خیلی نازک سطحی در یک زمان بسیار کوتاه ، به دمای استنیتی میرسد. حتی با پرتو لیزری که قدرت متوسط آن در حدود " W / Cm ۵۰۰ باشد، یک گرادیان حرارتی برابر C/mm° ۵۰۰ حاصل می شود. با حرکت دادن پرتو لیزر بر روی سطح قطعه، بخش های مورد نظر به سرعت گرم می گردند. سپس در اثر انتقال حرارت به داخل قطعه ، این نواحی سریع سرد میشوند. با انتخاب چگالی قدرت و سرعت حرکت مناسب برای پرتو لیزر ، قطعه را می توان تا عمق مورد نظر سخت کرد. زمان گرم کردن برای رسیدن سطح قطعه به دمای استنیتی ، می تواند، در حدود کمتر از یک ثانیه تا حدود چند ثانیه تغییر کند.
لیزر را می توان برای برش قطعات و یا جوشکاری آنها نیز مورد استفاده قرار داد. [3]
کاربرد
به علت دقت بسیار بالا و منطقه ی HAZ کوچک از لیزر برای سختکاری سطوح پیچیده چرخ دنده ها، لبه های قالب های پیچیده، تیغه های پیچیده و دیگر مقاطع حساس استفاده می شود.
امروزه از همین ویژگی برشی پرتو لیزر برای ساخت قطعات سرامیکی دقیق و پیچیده به روش لایه لایه ای استفاده میکنند. در این روش ، با مخلوط کردن پودر سرامیک با یک مایع مناسب، ماده سرامیکی را به صورت خمیر نرم در آورده و سپس با نورد کردن آن، ورقه های نازک سرامیکی تهیه می کنند. در مرحله بعد، با قرار دادن لایه های نازک ، مطابق یک مدل کامپیوتری بر روی یکدیگر، و تنظیم فاصله کانونی پرتو لیزر، آخرین لایه را برش می دهند تا شکل پیچیده مورد نظر به دست آید.
قدرت مورد نیاز لیزر
چگالی قدرت پرتو لیزر برای برش قطعات و یا جوشکاری آنها، خیلی بیش از چگالی قدرت لیزر برای گرم کردن سطح قطعه می باشد. دانسیته قدرت برای عملیات حرارتی معمولاً در حدود W / Cm۲ ۱۰۰۰ - ۲۰۰۰ است که گاهی اوقات حداقل به W / Cm ۵۰۰ و حداکثر "W/Cm ۵۰۰۰ نیز می رسد. بطور کلی لیزرهائی که برای عملیات حرارتی سطحی به کار برده می شوند، بایستی پرتو آنها پخش تر و شدت شان کمتر باشد. ضخامت بخش سخت شده قطعات ، به ندرت از ۲ / ۵ میلیمتر تجاوز می کند. برای فولادهائی که دارای عمق نفوذ کم سختی هستند، مانند فولادهای کربنی ، ضخامت ناحیه سخت شده خیلی کمتر بوده و از ۰ / ۲۵ میلیمتر در فولادهای نرم تا ۱ / ۳ میلیمتر در فولادهای باکرین متوسط ، تغییر می کند. با توجه به اینکه سرعت گرم کردن و سردکردن دراین روش خیلی بالا است ، حتی فولادهانی مانند 1018 SAE را ، که قابل بدهی به روش معمولی نیستند ، می توان با پرتو لیزر مورد آبدهی قرار داد. بهمین دلیل نیز سختی حاصله از طریق لیزر می تواند کمی بیشتر از سختی به دست آمده با روش های متداول آبدهی باشد
سخت کردن سطح قطعه بوسیله لیزر را می توان با سخت کردن توسط مشعل تشبیه کرد، با این تفاوت اساسی که انرژی تشعشعی مشعل ، برخلاف لیزر، پیوسته نیست. یعنی آنکه نمی توان آنرا تا مسافت زیادی انتقال داد. همچنین، گرمای ناشی از مشعل به اطراف پخش می شود. در صورتی که لیزر اشعه ای متمرکز تولید میکند. بعلاوه انرژی منتقل شده از مشعل به قطعه ، کاملاً محدود است و اغلب از حدود " W
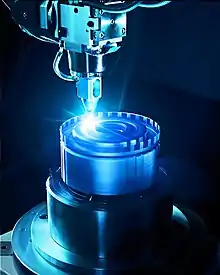
/ mm ۱ / ۶ تجاوز نمیکند ولی انرژی پرتو لیزر را میتوان ضمن کنترل اندازه سطح مقطع اشعه ، بسیار بیش از این حد (تا ۵۰۰ برابر) مورد استفاده قرار داد. به علاوه قدرت کم مشعل باعث می شود که گرما تا اعماق قطعه نفوذ کند، در صورتیکه در همین حال، دمای سطح بتدریج تا دمای مورد نظر افزایش می یابد. همچنین، گرم شدن و سرد کردن غیر یکنواخت قطعه و یا شوک های حرارتی ، در حین عملیات سرد و گرم گردن ، نیز می تواند موجب ترک و پیچش در آبدهی قطعه با مشعل شود. [4]
مزیت ها
مزیت برسختکاری القایی
سخت کردن بطریق القائی ، گرچه دارای قدرتی نزدیک به قدرت پرتو لیزر است ، ولی جریان القائی ، حتی در فرکانس های بالا ، تا اعماق قابل توجهی از سطح قطعه نفوذ مینماید. لذا در این روش نیز مقداری حرارت اضافی تولید می شود که لازم است با سرد کردن سریع از بین برود، در نتیجه قطعه تحت شوکهای حرارتی شدید قرار خواهد گرفت.
همچنین، در فرایند سخت کردن القائی ، اندازه قطعات نیز یک عامل بحرانی است. حلقه مارپیچی باید کاملاً مناسب شکل و ابعاد قطعه بوده و نیز تغییرات فاصله تا حدود ۱ میلیمتر بین حلقه مارپیچی و سطح کار می تواند بر نتیجه عملیات و یکنواختی آن بگذارد. ولی انجام عملیات حرارتی با سیستم های لیزری . به علت عمن کانونی زیاد پرتو لیزر ، می توند با همان شدت تا فاصله قابل توجهی صورت گیرد. در نتیجه عملیات حرارتی قطعه ، به فاصله بین قطعه و منبع حرارت حساسیت کمتری دارد.
مسئله دیگر در انجام عملیات حرارتی بطریق القانی ، تغییر خواص مغناطیسی قطعه در هنگام گرم کردن آن میباشد. به این دلیل باید فرکانس را تغییر داد تا گرم کردن قطعه دارای بازدهی کافی باشد. در عین حال وقتی قطعه تا بالای نقطه کوری گرم شود ، پای امنیتیک شده و عمق نفون نیز افزایش می یابد. ملاحظه می شود که از این نظر نیز با توجه به اینکه قابلیت بازدهی پرتو لیزر تحت تأثیر تغبیر ویژگی مغناطیسی فلعه قرار ندارد، این روش دارای ارزش اساسی است.
مزیت بر سختکاری ترموشیمیایی
در عملیات سطحی به روش ترموشیمیک ، سرعت دیفوزیون به نوع عناصر نفوذ کننده مانند ازت ، کربن، کروم ، نیکل و غیره و نیز دمای عملی بستگی دارد. در جریان این عملیات سطحی ، اجبار، تمام حجم قطعه گرم و سرد می شود. تأثیر گرم و سرد کردن های قطعه، همراه با تغییرات حجم ناشی از نفوذ عناصر آلیاژی ، موجب پیچش و تغییر أبعاد قلعه می شود. سرعت نفوذ را می توان با افزایش دمای تمام حجم قطعه بالا برد ، ولی در استفاده از اشعه لیزر می توان دمای سطح را افزایش داده و حتی یک لایه نازک سطحی را ذوب کرد، بدون آنکه تمام حجم قطعه گرم شود. افزودن عناصر آلیاژی ، به این لایه ذوب شده و می تواند موجب نفوذ سریع آنها به درون قطعه شود. تنوع عناصری که می توانند در این روش سریع و به آسانی به سطح ذوب شده اضافه شوند. مزیت مهم دیگر کاربرد پرتو لیزر می باشد. در جدول زیر، به عنوان مثال ، نوع و در صد بعضی از عناصر آلیاژی قابل افزودن به سطح قطعات ، توسط اشعه لیزر که تاکنون مورد بررسی و تحقیق قرار گرفتهاند . آمده است:
عنصر | C | Mn | V | W | Ni | Cr |
حداقل | 0.8 | 1.5 | 0.1 | 0.5 | 3 | 3 |
حداکثر | 3.5 | - | 1.5 | 9 | - | 50 |
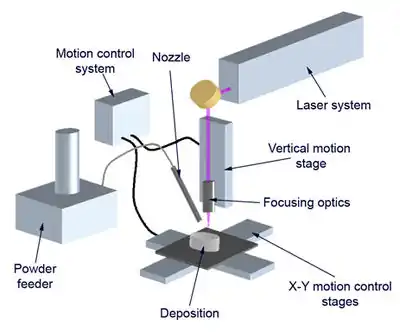
به این ترتیب ، با استفاده از قابلیت های پرتو لیزر، می توان قطعات را از چدن با فولاد ارزان ، با عملیات ماشینکاری ، تهیه کرده و سپس آنها را در سطح ، یا در بعضی از مواضع مورد نظر . آلیاژی کرد. این عملیات ، بدون نیاز به گرم کردن تمام حجم قلعه ، می تواند انجام گیرد.باید توجه داشت که قطعات فولادی ، از نظر قابلیت جذب پرتو مادون قرمز و زیر مادون قرمز خوب نمیباشند. از این نظر ، سطح صیقل شده آهن خالص، دارای قابلیت جذبی در حدود ۴ درصد، در دمای محیط ، است. یک سطح ساچمه کاری شده چدنی ، دارای قابلیت جذبی در حدود ۲۵ درصد می باشد. این قابلیت جذب، در ۸۰۰ درجه سانتیگراد به حدود ۴۰ درصد می رسد. تشکیل اکسیدها در روی سطح قطعات فولادی میتواند قابلیت جذب را افزایش دهد، ولی برای استفاده مزتر از پرتو لیزر، لازم است سطح قطعه توسط ماده ای با قابلیت جذب بالا پوشش داده شود. بدین منظور، پوشش های شیمیائی از قبیل فسفات منگنز، رنگ های گرافیت ، سیلیس و کربن با موفقیت مورد استفاده قرارگرفته اند. بعضی از این مواد ممکن است در جریان گرم کردن سوخته و از محیط عمل خارج شوند و از بعضی مواد دیگر نیز خاکستری باقی بماند. قابلیت جذب این پوشش ها، در ابتدای گرم کردن تا حدود ۹۰ درصد بوده و در ادامه عملیات نیز همواره قابلیت جذب آنها ، از قطعه بدون پوشش، بالاتر است. [5]
مشکلات
مشکلات عمده سختکاری با لیزر:
- عمق قابل سخت کاری با پرتو لیزر محدود بوده و حداکثر تا حدود ۲ / ۵ میلیمتر، و معمولاً تا نصف این مقداری می رسد.
- بهای تجهیزات زیاد می باشد، بنابراین ، لازم است ، در این روش بهای تمام شده محصول به دقت مورد ارزیابی قرار گیرد . سرعت زیاد گرم شدن قطعه با پرتو لیزر، مسئله تشکیل استنیت و توزیع مجدد کربن برای ایجاد محلول جامد همگن کربن در استنبت ، در زمان کوتاه را پیش می آورد. این مسئله ، در صورتی که ساختار قطعه شامل پرلیت درشت بوده و یا دارای سمانتیت پرواتکتوئید و یا سمانتیت کروی باشد و نیز در حالتی که چدن ، فریت زاد قابل توجهی داشته باشد، بارزتر است. لذا لازم است دمای استنیتی کردن قطعه، توسط لیزر کاملاً بالاتر از دمای آستنیتی کردن قطعه به روش های دیگر آبدهی انتخاب شود.
- موضوع دیگری که در انجام بعضی از عملیات با پرتو لیزر بدان برخورد می شود آنست که در جریان گرم شدن قطعه با پرتو لیزر ، انتقال جانبی حرارت غیر قابل احتراز است. هر قدر سرعت حرکت پرتو لیزر کمتر باشد اثر انتقال حرارت به اطراف نیز بیشتر خواهد بود. برای بسیاری از کاربردها ، بشرط آنکه عملیات طوری صورت گیرد که نواحی گرم شده قطعه و اطراف آن تحت فرسایش، با تنش های قابل توجهی در هنگام کار قرار نگیرند، تشکیل چنین ناحیه ای زیان بخش نیست.
عوامل مؤثر در عملیات سطحی با لیزر
عوامل متعددی ، از قبیل اندازه قطر پرتو لیزر ، دانسیته ندرت ، سرعت حرکت اشعه ، ویژگی های حرارتی جسم و قابلیت سخت شدن آن با لیزر ، بر روی نتایج حاصله از عملیات سطحی با لیزر اثر می گذارند. قابلیت سخت شدن با پرتو لیزر ، به سرعت گرم شدن جسم و نیز به حالت اولیه قلعه ، یعنی حالت نرمالیزه ، بازپخت شده و غیره بستگی دارد.
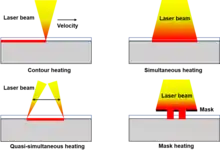
از عوامل اصلی موثر در عملیات حرارتی با لیزر، چگالی قدرت و سرعت اجرای عملیات میباشند. مهم است به این نکته توجه شود که سرعت عملیات بایستی تا حد امکان بالا باشد تا سرعت تولید افزایش یابد. با این حال، سرعت حرکت پرتو لیزر ، که به صورت حرکت لکه در روی سطح قطعه مشخص می شود، بخودی خود شاخص مناسبی برای سرعت تولید نمیباشد ، زیرا ابعاد لکه در جهت عمود بر امتداد حرکت پرتو لیزر نیز در تعیین میزان مساحت پوشیده شده دخالت دارد. بعلاوه، عامل مهم دیگر در تعیین نتایج عملیات به زمان باقی ماندن قطعه در زیر پرتو لیزر میباشد که عبارت از قطر لکه در امتداد حرکت، تقسیم بر سرعت حرکت است و معمولاً بنام زمان توقف با زمان سکون(۱) نامیده می شود. در موقعی که چگالی قدرت ثابت باشن تغییر ابعاد نسبی یک لکه مستطیل شکل ، بر روی میزان پوشش نامه ، اثر نمیگذارد. بنابراین ، مساحت لکه لیزر محدود به قدرت موجود منبع اشعه است.
توجه به نکات زیر، به عنوان راهنمای اجرای عملیات سطحی با لیزر، توصیه می شود
- - چگالی قدرت قابل استفاده در سخت کردن سطحی با لیزر معمولاً درحدود 'W/Cm ۵۰۰ تا '۵۰۰۰W/Cm انتخاب می شود. - زمان سکون بین ۰ / ۱ تا ۱۰ ثانیه تغییر میکند. برای فولادهای کربنی ، چگالی قدرت معمولاً بین 'Cm ..۱۰ تا"w/m ۱۵۰۰ و زمان سکون برابر ۱ تا ۲ ثانیه در نظر گرفته می شود.
- - مصالحی با قابلیت سختی پذیری بالا را می توان . با چگالی قدرت کم تر و زمان سکون بیشتر، تحت عملیات سخت کاری با لیزر قرار داد، در حالیکه مصالحی با قابلیت سختی پذیری کمتر را می توان با چگالی قدرت بیشتر و زمان سکون کمتر سخت کاری کرد.
- - استفاده از پرتو لیزر ، با مقطع مستطیلی یا مربعی ، با چگالی قدرت یکنواخت، برای به دست آوردن سختی همگن و مناسب تر می باشند.
- - چگالی قدرت بیشتر و زمان سکون کم تر، ضخامت سخت شده کم تر و سرعت بالاتر سرد شدن را تأمین می کند. برای چگالی قدرت کمنر ، نتیجه بر عکس می باشد.
- - حداکثر دمای سطح، متناسب با ریشه دوم سرعت حرکت اشعه میباشد . بنابراین، با دو برابر کردن چگالی قدرت بایستی این سرعت چهار برابر شود تا همان حداکثر دما در سطح تلعه حاصل گردد.
- - افزایش چگالی قدرت موجب کاهش انرژی کل ورودی ، برای بدست آوردن همان حداکثر دما در سطح قطعه ، میشود.
- - انتخاب زمان سکون به ساختار میکرسکپی فولاد نیز بستگی دارد. قطعات فولادی با ساختارهای نرمالیزه ، بازپخت شده با دارای پرلیت کروی و با حاوی سمانتیت پرواتکتوئید و نیز چدن با فولاد با کربورهای آلیاژی پایدار ، مثلاً در مقایسه با فولادی که قبلاً آبداده و بازگشت شده باشد، به زمان سکون های طولانی تری نیاز دارند.
- - برای قطعات کوچک و در مقایسه با قطعات بزرگتر، لازم است چگالی قدرت بالاتر و زمان سکون کمتری در نظر گرفته شود، مگر آنکه محیط سرد کننده خود جسم نبوده و قطعه در محیط دیگری سرد شود.
لیزر مورد استفاده در عملیات سطحی بر روی قطعات فلزی
لیزرهانی که اغلب برای انجام عملیات سطحی قطعات فلزی مورد استفاده قرار می گیرند، از نوع لیزر نودای میوم)، لیزر نوع جامد YAG( و یا لیزر گازی دی اکسید کربن ,co) می باشد. خروجی این لیزرها ممکن است بصورت پالسی با پیوسته باشد که هر دو نوع را می توان برای سخت کردن سطحی مورد استفاده قرار داد. با توجه به اینکه بهای یک سیستم لیزری تقریبأ متناسب با ماکزیمم قدرت خروجی آنست، کوچکترین اندازه یک واحد لیزری برای کاربرد سنعنی بایستی با توجه به عواملی از قبیل سرعت تولید، حداقل عملی برای اندازه تکه و دانسبته لازم قدرت برای حصول به نتیجه مورد نظر به تعیین گردد. باید یادآور شد که با این حال لیزر یک وسیله چند منظوره بوده و می تواند برای انجام عملیات دیگر بر روی فلزات ، از قبیل جوشکاری و برشکاری نیز مورد استفاده قرار گیرد.
پرتو لیزر . تشعشع های الکترو مغناطیسی در ناحیه مادون قرمز نیز انتشار می دهد. لیزر حاصله از گازکربنیک دارای طول موجی برابر ۱۰ / ۶ میکرون بوده و براحتی توسط بسیاری از مصالح غیر فلزی جذب می شود. قرار دادن یک قطعه نازک لوسیت)، بین شخصی عمل کننده و ناحیه کار، برای جلوگیری از اثرات مضر تشعشع ، کافی می باشد. نیزر YAG دارای طول موج خیلی کمتری ( 1.64 میکرون) است و بنابراین ، عمل کننده بایستی از عینک هایی با پوشش رنگ مخصوص استفاده کند. قدرت این لیزرها نسبتاً محدود است. بنابراین در مورد کار بر روی قطعاتی که نیازمند قدرتی بیش از ۵۰۰ وات می باشند ، لیزر گازکربنیکی معمولاً مورد استفاده قرار میگیرد، زیرا می تواند قدرت خروجی خیلی بالاتری را تأمین کند.
پرتو لیزر را معمولاً با یک سیستم نوری شکل و جهت میدهند نابعاد و شکل مورد نظر برای نکه حاصل شود. با توجه به اینکه کاهش قدرت تشعشع پیوسته لیزر با تغییر فاصله کوچک است، لذا منبع لیزر را می توان در فاصله قابل توجهی از قلعه قرار داد.
در عملیات جوشکاری و برشکاری ، یک دسته پرتو کانونی شده با قدرت زیاد ، بکار می رود. برای انواع عملبات سخت کاری که با دگرگونی فازی همراه است ، از پرتو پهن تر، با چگالی قدرت خیلی کمتر استفاده می شود. یک علت این امر آن است که فراینده سخت کاری، در این حالت نیازمند چگالی ندرت کمتری است تا سرعت روییدن مناسبی را برای سطح قطعه تأمین کند.
اجزاء نوری از قبیل عدسی و دیافراگم ، که در استفاده از لیزر گازی بکار می روند، بایستی با توجه به طول موج بلند این لیزرها از مواد خاصی از قبیل سلنید روی) باشند تا از جذب زیاد تشعشع جلوگیری گردد. اجراء نوری انعکاسی کمتر شکننده بوده و برای موارد کاربرد صنعتی ، انطباق بیشتری دارند. این اجزاء شامل آینه های مسلح ،کروی با سهموی هستند که از مس یا مولیبدن ساخته شده و دارای قدرت انعکاسی عالی برای پرتو های لیزر می باشند.
جستار های وابسته
پانویس
- "سخت کردن سطحی". ویکیپدیا، دانشنامهٔ آزاد. 2019-06-01.
- "عملیات حرارتی موضعی". ویکیپدیا، دانشنامهٔ آزاد. 2020-03-07.
- مهدي طاهري، اصول عمليات حرارتي فولادها، 655.
- مهدي طاهري، اصول عمليات حرارتي فولادها، 657.
- رحيم زمانيان، خوردگي و روش هاي كنترل آن، 405.
فهرست منابع
- طاهري، مهدي (۱۳۹۶). اصول عمليات حرارتي فولاد ها. انتشارات دانشگاه تهران. شابک ۹۷۸-۹۶۴-۰۳-۳۹۶۸-۸.
- زمانیان، رحیم (۱۳۹۶). خوردگی و روش های کنترل آن. انتشارات دانشگاه تهران. شابک ۹۷۸-۹۶۴-۰۳-۵۳۷۹-۰.
- C. Suryanarayana, Nanostructured Intermetallics in Intermetallic Compounds - Principles and Practice, John Wiley & Sons, pp.749-764, 2002. doi:10.1002/0470845856.ch35
- مرادپور، محسن (۱۳۸۱). «سختکاری سطحی موضعی یا انتخابی». صنعت خودرو. ۵ (۵۴): ۴۰تا ۴۲.