پوششدهی
پوشش دهی، به فرآیند پوشش دادن بر روی سطح اشیا گفته میشود. در بسیاری از موارد کاربرد آلیاژهای گرانقیمت مقاوم در مقابل خوردگی عمل چندان صحیحی نیست، بلکه از لحاظ اقتصادی استفاده از فولادهای کم کربن ساده به دلیل قیمت پایین و قابلیت تغییر شکل آسان ارجحیت دارد. در این گونه موارد توصیه میشود که سطح قطعات فولادی را با استفاده از پوششهای سطحی در مقابل خوردگی محافظت شود.[1]
کاربرد پوششها معمولاً به منظور اهداف متفاوتی از قبیل افزایش سختی، مقاومت سایشی، مقاومت خوردگی، هدایت حرارتیوالکتریکی، قابلیت انعکاس نور و رنگ است. در انتخاب ماده پوشش علاوه بر توجه به خواص مورد نظر در ارتباط با کاربرد ان باید عوامل اقتصادی هم مورد توجه قرار بگیرد. برای مثال برای بسیاری از مواد فولادی میتوان از آلومینیوم استفاده کرد زیرا وزن کم و مقاومت به خوردگی خوبی با تشکیل یک لایه اکسیدی برای محافظت از قسمتهای زیرین دارد ولی یک عیب دارد و ان هم استحکام پایین آلومینیوم خالص است بنابراین از آلیاژهای مختلف آلومینیوم که استحکام بالایی دارد استفاده میشود اما این عناصر آلیاژ هم عیوبی اضافه میکنند که ان هم مقاومت در برابر خودگی را کاهش میدهد. برای افزایش سختی سطح و مقاومت به خوردگی میتوانیم از ترکیب از دو روش بالا استفاده کرد به این صورت که ابتدا با عناصر آلیاژی سختی فولاد مورد نظر را بالا میبریم و بعد با یک پوشش نازک آلومینیوم در برابر خوردگی تنشی و تورقی مقاوم میکنیم. این لایه نازک اکسید آلومینیوم را میتوان از روش آندکاری یا آندایزینگ استفاده کرد.
همچنین میتوان از مس و آلیاژهایی نام برد که به دلیل قابلیت هدایت الکتریکی بالا در سوییچهای الکتریکی یا دستگاههای تقویت کننده به کار میرود، ولی به مرور زمان در اثر واکنش با محیط اطراف سطح ان تیره میشود و موجب ایجاد اختلاف در اتصال میشود. بدین جهت در مواردی برای جلوگیری از این پدیده پوشش بسیار نازکی از طلا بر روی اتصالات داده میشود.
موادی که در لایههای پوششی استفاده میشود، میتواند از مواد فلزی، سرامیکی و پلیمری باشد. معمولاً چسبندگی بین لایه پوشش و ماده اصلی باید به اندازهای باشد که لایهٔ پوشش بتواند کاملاً محکم بر روی ماده اصلی بچسبد و خواص مطلوی را در سطح خارجی ان به وجود آورد.
روشهای پوشش دهی
پوشش دهی با استفاده از روشهای متعددی از قبیل:
- روکش کاری فلزی[2]
- روش نفوذی
- غوطه وری در مذاب
- رسوب دادن الکتریکی
- رسوب دادن بخار
- روش پاشیدنی
انتخاب روش و خواص حاصل از پوشش به جنس لایه پوشش و ماده اصلی بستگی دارد.
پوشش دهی در حالت جامد
پوشش دهی در حالت جامد معمولاً از طریق روش مکانیکی با استفاده از عملیات تغییر شکل گرم (مانند نورد، اکستروژن[3] و فورجینگ) انجام میگیرد. برای مثال لایه پوشش به صورت ورق نازکی بر روی ورق دیگری قرار داده میشود و در دمای معین تحت عملیات نورد قرار میگیرد. اتصال این دو ورق به یکدیگر در نتیجه فشار غلتکها و سیلان هم جهت دو فلز در تغییر شکل پلاستیکی صورت میگیرد. نورد در درجه حرارت بالا سبب اتصال قویتر آنها به یکدیگر در نتیجه نفوذ متقابل اتمها در سطح تماس آنها میشود. در این نوع پوشش دهی در بعضی از ترکیبات امکان تشکیل فاز بین فلزی ترد وجود دارد. تشکیل آیت فازهای ترد میتواند در چسبندگی لایهها در حین تغییر شکل خلل ایجاد کند که موجب ظاهر شدن ترکهایی در سطح میشود.
پوشش دهی از طریق غوطه وری
در این روش پوشش دهی بدین صورت انجام میگیرد که ماده پوشش تا رسیدن به حالت مذاب حرارت داده میشود و سپس قطعه مورد نظر برای مدت کوتاهی در این مذاب غوطه ور میشود. در این عملیات ماده پوشش میتواند در داخل ماده اصلی نفوذ کند و در مورد فلزات آلیاژی را به وجود آورد. ضخامت لایه پوشش به فلزات تشکیل دهنده آلیاژ، درجه حرارت و مدت نگهداری در مذاب بستگی خواهد داشت.
روش رسوب دهی الکترولیتی
این روش که به نام گالوانیزه کردن نیز معروف است، برای پوشش دهی قطعاتی به کار میرود که دارای قابلیت هدایت الکتریکی هستند. در این روش قطعه در محلول الکتریکی که دارای فلز مورد نظر برای پوشش دهی باشد قرار داده میشود. رسوب فلز بر روی سطح قطعه طبق واکنش زیر انجام میگیرد:
یون مثبت فلز + الکترون = فلز به صورت اتمی
لایه رسوب و ضخامت ان
چگونگی لایه رسوب و ضخامت ان به عواملی از قبیل ترکیب شیمیایی الکترولیت، درجه حرارت، مدت زمان عبور جریان، شدت جریان بستگی دارد. ضخامت لایه پوششی را میتوان به آسانی با تنظیم و کنترل عوامل مؤثر تغییر داد.
پوشش میتواند از یک لایه یا چندین لایه ساده یا آلیاژی انتخاب شود. برای مثال برای سپر ماشین از یک لایه پوشش داخلی از مس برای چسبندگی خوب، یک لایه میانی از نیکل برای حفاظت از خوردگی و یک لایه خارجی نازک از کروم برای زیبایی خارجی سپر استفاده میشود. در روش الکترولیتی اتمهای هیدروژن ایجاد شده میتواند در داخل لایه پوشش یا در داخل فلز اصلی زمینه نفوذ کند و موجب پایداری ترکیبات بین فلزی ترد در محدوده سطح تماس دو لایه و در نتیجه شکست ترد شود. در چنین مواردی برای رفع این مشکل لازم است عملیات حرارتی خاص به منظور هیدروژن زدایی از سطح خارجی قطعه انجام گیرد.
جنس مواد پوششی در روش الکترولیتی
جنس مواد پوششی قابل استفاده در این روش میتواند از فلزات مانند روی، کادمیم، سرب و آلیاژهای ان، نیکل و آلیاژهای ان، مس و آلیاژهای ان، طلا و آلیاژهای ان، قلع و آلیاژهای ان، پلاتین و رودیم میتواند به عنوان مواد پوششی انتخاب شود.
اغلب برای تشکیل لایه محافظ که بتواند کاملاً محکم به سطح ماده اصلی بچسبد لازم است از چندین لایه پوشش متفاوت استفاده شود.
پوشش دهی از طریق رسوب دادن بخار
این روش به صورت فیزیکی و هم شیمیایی صورت میگیرد که در ان مواد از حالت بخار بر سطح ماده دلخواه نفوذ داده میشوند. خواص این نوع پوشش با دیگر روشها متفاوت است؛ بنابراین میتوان پوششهای فلزی با خلوص فوقالعاده و با ضخامتهای کم به صورت براق حتی با ساختار شیشهای بدست آورد. عملیات رسوب دادن بخار در خلأ میتواند بر روی مواد فلزی و غیر فلزی انجام گیرد.
رسوب دادن فلزهای گرانقیمت بیشتر کاربردهای تزیینی دارد. کاربردهای دیگر این روش در صنایع الکتریکی، الکترونیکی و در زمینه هوا-فضا است، جایی که پوششهای حفاظتی فوقالعاده نازک با درجه خلوص و حفاظت بالا مورد نظر است. یکی از مزایای این روش حذف تولید هیدروژن در ان و در نتیجه پایدار نگشتن شکست ترد در ماده اصلی است. بدین دلیل این روش پوشش دهی کاربرد وسیعی در حفاظت از خوردگی فولادهای آلیاژی با استحکام بالا با عناصر روی و کادمیم در شرایط محیط کاری با تنشهای بالا دارد.
پوشش دهی از طریق پاشش
روش پاشش یکی دیگر از روشهای پوشش دهی سطحی است. در این روش نه تنها فلزات بلکه مواد سرامیکی و پلیمری را هم میتوان پوشش داد. این روش بر حسب چگونگی گرم کردن و اعمال ماده پوشش بر روی سطح قطعه میتواند به صورتهای مختلفی انجام گیرد.
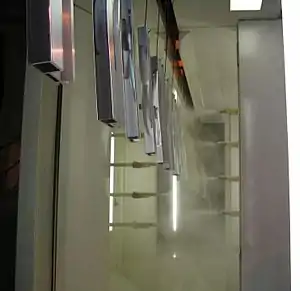
پاشیدن شعلهای
در پاشش شعلهای ماده به صورت مفتول یا پودر به کمک شعله گاز اکسیژن و استیلن یا پروپان ذوب و با فشار هوا به صورت ذرات ریز بر روی قطعه پاشیده میشود.[4]
پاشیدن قوسی
در پاشیدن قوسی از دو مفتولی که از جنس ماده پوشش است، به عنوان الکترود استفاده میشود. سپس با ایجاد قوس الکتریکی بین آنها و تبدیل ماده پوشش از حالت جامد به مذاب به کمک فشار هوا بر روی سطح قطعه مورد نظر پاشیده میشود.
پاشیدن پلاسمایی
روش پاشش پلاسمایی شباهت زیادی به پاشش قوسی دارد. در این روش قوس الکتریکی برای ذوب و به حالت اتمی درآوردن ماده پوشش به کار میرود. پلاسمای ایجاد شده در قوس الکتریکی بر روی سطح قطعه پاشیده میشود. این لایههای پوششی به منظور حفاظت از خوردگی، جلوگیری از ایجاد پوستههای اکسیدی در مجاورت هوا در دمای بالا و فرسایش و مچنین برای تولید قالبها و بهبود قطعات چدنی ریختهگری شده به کار میرود.
ساختار لایه پوشش
ساختار میکروسکوپی لایه پوشش به سرعت سرد شدن ان لایه بستگی دارد. بدین ترتیب در لایه پوشش میتواند فازهایی تشکیل شوند که در حالت تعادل نباشند.
در مواد سرامیکی و پلیمری احتمال تشکیل ساختار شیشهای زیاد است، در حالی که در مخلوطی از اتمهای فلزی فازهای محلول نیمه پایدار ایجاد میشود. این فازهای نیمه پایدار میتوانند به حالت تعادل در ایند. بدین ترتیب پایداری حرارتی لایه پوشش محدوده حرارتی کاربرد لایه پوشش را در دماهای بالا تعیین میکند.
چگونگی تولید لایههای سرامیکی مقاوم در دماهای بالا در تکنولوژی مواد در درجه حرارتهای بالا نقش مهمی را ایفا میکند. برای مثال به وسیلهٔ تزریق شعلهای میتوان لایههای پوششی از مواد با نقطه ذوب تا ۲۵۰۰ درجه سانتیگراد بر سطح قطعات اعمال کرد، بدون اینکه حرارت بعدی ماده اصلی لازم باشد. با استفاده از روش تزریق پلاسما میتوان به درجه حرارتهایی تا ۲۰۰۰۰ درجه سانتیگراد دست یافت و بدین ترتیب مواد سرامیکی با نقطه ذوب بالا را نیز به عنوان لایههای پوششی به کار برد.[5]
پوشش با مواد پلیمری
یکی از روشهای ارزان قیمت برای حفاظت از خوردگی استفاده از مواد پلیمری با رنگهای گوناگون است. مواد رنگی میتواند تا حدودی فلزات را از خوردگی محافظت کند. البته رنگ آمیزی نه فقط به عنوان محافظ، بلکه در مواردی برای تزیین قطعات نیز به کار میرود. سرنج یکی از رنگهایی است که حالت قلیایی داشته و از خردگی در سطح فلز جلوگیری میکند؛ ولی اثر ان بعد از مدتها کم میشود و باید هر چند یکبار انجام گیرد.
فسفاته کردن
در این روش قطعات فولادی را با غوطه ور ساختن در وان حاوی محلولهای فسفات پوششهای فسفاتی داده میشود. پوششهای فسفاتی اکثراً برای ایجاد زمینه مناسب برای رنگ آمیزی روی قطعات به کار میرود.
منابع
- https://en.wikipedia.org/wiki/Coating#cite_ref-.3F_2-0
- http://www.inovati.com/information/Technology/km.php
- http://www.packaging-int.com/video/Slot-Curtain-Coating.html بایگانیشده در ۲۲ مه ۲۰۱۲ توسط Wayback Machine Slot die coating animations
- https://en.wikipedia.org/wiki/Powder_coating
- http://performancecoatings.com/
- High-Performance Organic Coatings, ed. AS Khanna, Elsevier BV, 2015, ISBN 978-1-84569-265-0
- Coating Materials for Electronic Applications: Polymers, Processes, Reliability, Testing by James J. Licari; William Andrew Publishing, Elsevier, ISBN 0-8155-1492-1
- SPI - industrial coating technologies and products
- S. Grainger and J. Blunt, Engineering Coatings: Design and Application, Woodhead Publishing Ltd, UK, 2nd ed. , 1998, ISBN 978-1-85573-369-5
- http://www.masterbond.com/applications/corrosion-resistant-epoxy-coatings