قالبگیری بادی
قالبگیری بادی (به انگلیسی: Blow molding) یک فرایند تولید است که در تولید قطعات پلاستیکی توخالی مانند بطریهای پلاستیکی به کار میرود. قالبگیری بادی به سه صورت انجام میشود: قالبگیری بادی اکستروژن، قالبگیری بادی تزریقی، قالبگیری بادی تزریق کششی.
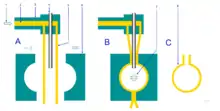
فرایند قالب گیری بادی با گرم کردن پلاستیک و ایجاد لقمه اولیه آغاز میشود، لقمه اولیه به صورت یه استوانه یک سر آزاد دارای روزنه است که هوا میتواند از آن عبور کند، سپس لقمه داخل قالب قرار میگیرد و باد در آن دمیده میشود، فشار باد پلاستیک را هل داده و به دیواره قالب میچسباند، پس از خنک شدن پلاستیک و سرد شدن آن قالب باز شده و قطعه خارج میشود. در دو روش دیگر لقمه از تزریق در قالب مخصوص ایجاد میشود در مرحله دمیده شدن روش آخر یعنی قالبگیری بادی تزریقی کششی یک میله لقمه گرم شده را میکشد و در همین حال هوا در آن دمیده میشود.
تاریخچه قالبگیری بادی
ایده این روش در اصل از ایده دمیدن در شیشه مذاب آمدهاست. قالبگیری بادی مواد پلاستیکی در اواخر سالهای ۱۸۸۰ شروع شد و بین سالهای ۱۹۳۰ تا ۱۹۴۰ کمپانی Hartford Empire قطعاتی همچون تزئینات درخت کریسمس را تولید کردند. تا اواخر ۱۹۴۰ تیراژهای تولید محدود بودند و به همین خاطر این روش گسترش چندانی پیدا نکرد، هنگامی که تیراژهای تولید افزایش یافتند این روش گسترش یافت. مکانیزمهای مورد نیاز برای ایجاد قطعات تو داخلی در گذشته ساخته شده بودند و پس از اختراع پلاستیک، شیشه که بسیار شکننده است در بعضی کاربردها با پلاستیک جایگزین شد. اولین بار تولید انبوه بطریهای پلاستیکی در سال ۱۹۳۹ در آمریکا انجام شد، به فاصله کمی آلمان شروع به استفاده از این فرایند کرد و اکنون از پیشتازان این فرایند میباشد.
انواع قالبگیری بادی
۱- قالبگیری بادی اکستروژن
۲ – قالبگیری بادی تزریقی
۳- قالبگیری بادی کشش تزریقی
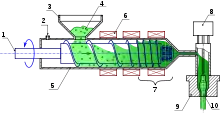
قالبگیری بادی اکستروژن
در این روش پلاستیک ذوب شده و سپس به شکل لقمه اکسترود میشود سپس این لقمه به داخل قالب رفته و باد داخل آن با فشار دمیده میشود، پس از سرد شدن قالب باز شده و قطعه خارج میشود. این فرایند به دو صورت انجام میشود یکی پیوسته و یکی متناوب، در فرایند پیوسته گرانولهای پلاستیک بهطور پیوسته اکسترود شده و لقمههای اولیه تولید میشود، سپس وارد قالب شده و در آنها هوا با فشار دمیده میشود. در فرایند متناوب ابتدا رزوه بالای لقمه ایجاد شده سپس با تزریق لقمه ایجاد میشود و سپس در آن دمیده میشود. در قالبگیری پیوسته وزن لقمه باعث تغییر ضخامت آن میشود و یجاد ضخامت یکنواخت را دشوار میسازد، برای حل این مشکل با سیستمهای هیدرولیکی به سرعت لقمه را از قالب خارج میکنند تا اثر وزن بر روی ضخامت دیوارهها حداقل شود.
برای مثال بطریهای شیر، بطریهای شامپو و آب پاشها با این روش تولید میشوند.
مزیت این روش هزینه پایین ابزار آن، سرعت تولید بالا و قابلیت ایجاد قطعات پیچیدهاست.
معایب این روش محدود بودن به قطعات تو داخلی و استحکام پایین قطعات تولیدی است
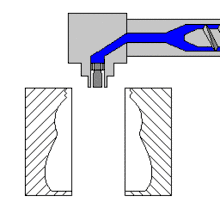
قالبگیری بادی تزریقی
این روش برای تولید انبوه قطعات تو خالی شیشهای و پلاستیکی به کار میرود. در این روش لقمه اولیه با تزریق درست شده و سپس باد داخل آن دمیده میشود، این روش کمتر از بقیه روشهای قالبگیری بادی استفاده میشود و بیشتر برای تولید ظروف یکبار مصرف داروها به کار میرود. بهطور خلاصه این فرایند به ۳ بخش: تزریق، دمیدن، بیرون انداختن.
در این فرایند ابتدا گرانولهای پلیمر در اکسترودر ذوب شده سپس با یک نازل داخل یک قالب تزریق میشود و لقمه ایجاد میشود سپس این لقمه از قالب خارج شده و داخل قالبی دیگر قرار میگیرد تا باد در آن دمیده شود، پس از سرد شدن قالب باز شده و قطعه خارج میشود.
قطعه نهایی با توجه به اندازه خود میتواند از ۳ تا ۱۶ حفره داشته باشد. برای خارج کردن قطعه از قالب معمولاً از ۳ پین پران استفاده میشود.
مزایا: دقت بالا
معایب: بیشتر در تولید بطریهای کوچک استفاده میشود زیرا کنترل فرایند دمیدن در ابعاد بزرگ دشوار است، به علت کشیده شدن پلاستیک، قطعات تولید شده استحکام بالایی ندارد.
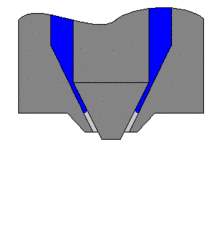
قالبگیری بادی کشش تزریقی
این روش خود به دو روش متفاوت یک مرحلهای و دو مرحلهای تقسیم میشود. در روش دو مرحلهای ابتدا پلاستیک به شکل لقمه اولیه در میآید، پس از خنک شدن برای آماده شدن برای مرحله بعد دوباره تا دمایی بیشتر از دمای انتقال شیشهای (با تابش فروسرخ) گرم شده سپس در داخل قالب قرار میگیرند و همواره یک ماهیچه لقمه کشیده نگه میدارد و هوا با فشار در آن دمیده میشود.
مزایا: قابلیت ایجاد قطعات حجیم، محدودیت کم در طراحی بطریها، امکان فروش لقمههای تولید شده در ابتدا به دیگر کارخانهها (بر خلاف فرایند قالبگیری بادی اسکتروژن).
معایب: فضای زیادی نیاز دارد، هزینه بالایی دارد.
در روش تک مرحلهای تولید لقمه و بطری نهایی در یک دستگاه انجام میشود و این کار هزینهها را تا ۲۵ درصد نسبت به روش قبلی که در آن لقمهها باید دوباره گرم شوند کاهش میدهد. در توضیح این روش باید گفت که فرض کنید مولکولها، توپهایی هستند که فضای خالی زیادی بین آنها وجود دارد و همچنین سطح تماسی کمی دارند حال با کشیدن در راستای عمود و سپس در راستی افق این ساختار به صورت ضربدری قرار گرفته و این باعث میشود که سطح تماس زیاد شده و فضای خالی کاهش میابد این باعث میشود که استحکام نهایی قطعه تولیدی افزایش یابد.
مزایا: از آنجا که لقمه سرد نمیشود امکان ایجاد مقاطع مستطیلی و غیر دایرهای با ضخامت یکسان وجود دارد.
معایب: در طراحی بطری محدودیتهایی وجود دارد.
جستارهای وابسته
منابع
ویکیپدیا انگلیسی (Blow molding)
Extrusion Blow Molding Technology, Hanser Gardner Publications, ISBN 1-56990-334-4