آزمایش خستگی
در حالی که برای طراحی قطعاتی که تحت بارهای استاتیکی قرار میگیرد حد تسلیم ماده از مهمترین کمیتهای مکانیکی است، برای اجزایی مانند محور توربینها با میل گاردانها، فنرهای معلق و فنرهای سوپاپ و از این قبیل که تحت تنشهای متناوب قرار میگیرند، بررسی تنش دیگری غیر از حد تسلیم مورد نیاز است. زیرا اگر این گونه قطعات تحت تأثیر نیروهای متناوب قرار گیرند پس از مدتی میشکنند هرچند که تنشهای وارد بر آنها بسیار پایینتر از استحکام کششی یا حد تسلیم باشد. پدیدهای را که در نتیجهٔ تنشهای متناوب در جسم ایجاد گشته و به شکست آن می انجامد، خستگی یا فرسودگی می نامند. هر چه تعداد تناوب تنشهای وارده بیشتر باشد، تنش شکست آن کوچکتر است. تنش متناوبی میتواند ناشی از چرخش، خمش یا ارتعاش باشد.[1]
![]() | این نوشتار نیازمند پیوند میانزبانی است. در صورت وجود، با توجه به خودآموز ترجمه، میانویکی مناسب را به نوشتار بیفزایید. |
حداکثر تنشی را که قطعهای از ماده معین بتواند به ازای آن تعداد دور فوق العاده زیادی را بدون اینکه بشکند تحمل کند، استحکام خستگی یا حد خستگی یا حد تحمل نامند.[2]
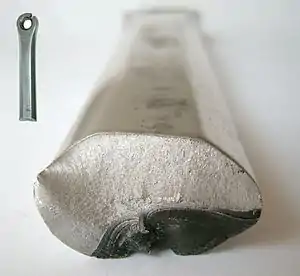
انواع آزمایشهای خستگی

دو نوع ازمایش خستگی انجام میگیرد که عبارتند از:
- ازمایش با فرضیات سادهکننده که تنش کششی و فشاری در هر سیکل با هم برابر باشند و تنش میانگین برابر صفر باشد.
- نمونه مورد ازمایش را درون وسایل ازمایش که تنش کششی و فشاری قابل تعیین است بنابراین تنش میانگین صفر نمیباشد و در اصل نمودارهای تنش وارده مانند شکل روبرو خواهند بود که کاملاً به صورت سینوسی یا کسینوسی نمیباشد.
چگونگی انجام ازمایش
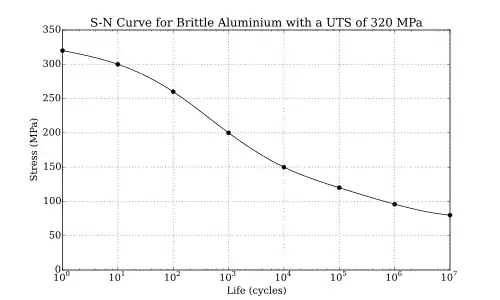
ویژگی نمونه مورد آزمایش
به منظور به دست آوردن حد تحمل نمونههایی از ماده مورد نظر، که همگی به صورت استاندارد شده دارای یک شکل، سطح مقطع دایرهای شکل، ابعاد مشخص شده، بدون عیب و با شرایط یکسان باشند، را انتخاب میکنیم.
با اعمال بار (به صورت خمشی) به نمونهها در یکی از دستگاههای آزمایش خستگی بلافاصله در سطح بالایی نمونه تنش کششی و در سطح زیری تنش فشاری ایجاد میشود. بعد از اینکه نمونه نیم دور (180 درجه) چرخید، موضعی که ابتدا تحت تأثیر تنش کششی قرار گرفته بود، اکنون تنش فشاری به آن اعمال میشود. بنابراین تنش در هر نقطهای از نمونه به صورت دور تناوب سینوسی کامل، تغییر میکند. تنش متناوبی میتواند بین دو مقدار حداکثر و حداقل در حالتهای مختلفی از کشش یا فشار تغییر کند. حالت اول تغییرات بارگذاری میتواند به گونهای باشد که تنش اعمالی بین دو مقدار تنش (کششی) وتنش (فشاری) تغییر کند و تنش متوسط میانگین ان دو میباشد . حالت دوم تغییرات تنش میتواند به صورتی باشد که حداکثر تنش در موقعیت فشاری کمتر از حداکثر تنش کششی باشد . در حالتهای دیگر باردهی به گونهای باشد که مقدار تنش بین حداکثر و حداقلی در موقعیت کششی یا فشاری تغییر کند.تنشهای اعمال شده نباید هر دو به صورت فشاری باشند زیرا تنشهای فشاری باعث بسته شدن ترکها میشود بنابراین شکست رخ نمیدهد پس حداقل باید یکی از تنشها کششی باشد.در بسیاری از حالتها به تنش متناوبی میتواند مقداری تنش دائمی به صورت استاتیکی افزوده شود. در هر صورت روابط زیر را میتوان برای تنش متناوبی تعریف کرد:
- تنش میانگین برابر حاصل جمع تنشهای فشاری و کششی تقسیم بر دو میباشد.
- تنش در هر لحظه برابر حاصل جمع تنش اولیه با معادله سینوسی تنش میباشد.
حداکثر تنش اعمال شده به نمونه آزمایش خستگی، به پارامترهای زیر وابسته است:
- نیروی وارده
- طول نمونه
- قطر نمونه
بعد از تعداد دور معینی شکست در نمونه ظاهر میشود. سپس مقادیر بدست آمده برای تنش و تعداد دور تا لحظه شکست را دریک سیستم محورهای مختصات با محورهای ساده (تنش) و لگاریتمی (تعداد دور) مشخص میکنیم. نقاط بدست آمده عملاً همگی بر روی یک منحنی قرار نگرفته، بلکه بیشتر در محدودهای کم و زیاد میشود. تعداد معدودی از نقاط بدست آمده از نمونههای آزمایش (حتی در شرایط یکسان آزمایش) میتوانند تفاوت بسیار زیادی از نقاط دیگر داشته باشد که معمولاً حذف میشوند. اکنون بر حسب حساسیت کاربرد ماده میتوان با استفاده از نقاط بدست آمده یک منحنی به نام منحنی ولر یا منحنی تنش – تعداد دور را رسم کرد. برای مثال منحنی را میتوان با استفاده از مقدار متوسط از مقادیر مشخص شده به وسیله آزمایش رسم کرد. این بدین معنی است که احتمال اینکه تمام نمونهها به ازای حد معینی از تنش تعداد دور تناوب مربوط به آن را بدون شکست بتوانند تحمل کنند، 50 درصد است.
طول عمر خستگی مشخصکننده مدت زمان سرویس دهی قطعهای است که تنش تناوبی معینی به آن اعمال میشود. برای مثال اگر تنش متناوبی به اندازه 620 مگاپاسکال به قطعه فولادی اعمال شود، طول عمر خستگی آن 100000 دور (چرخه) خواهد بود. در آزمایش مواد مختلف دو نوع منحنی بدست میآید. در یک نوع از آن منحنی (1) به ازای تعداد 1000000-10000000 دور تناوب به حد تنشی خواهد رسید که اغلب فولادهای نرم، آلیاژهای منیزیم و تیتانیم و بعضی از آلیاژهای آلومینیم از این نوع هستند. در نوع دیگر تعدادی از فلزات غیرآهنی از قبیل آلیاژهای مس، بعضی از آلیاژهای منیزیم و آلومینیم چنین حد کاملاً مشخصی ظاهر نمیشود، بلکه کاهش پیوسته تنش به ازای افزایش دوره تناوب دیده میشود، در این حالت تعیین حد تحمل چندان ساده نخواهد بود. اما از آنجایی که دادن کمیتی که بتواند حد خستگی یک ماده را مشخص کند از نظر صنعتی اهمیت دارد، لذا در این گونه موارد تنشی را که به ازای آن حدود 100 میلیون دور تناوب هنوز قابل تحمل باشد به عنوان حد تحمل انتخاب میشود. البته آزمایش بدین طریق صورت میگیرد که برای موادی که حد تحمل دارد با تنشی حدود 0.66 استحکام کششی استاتیکی ماده آغاز میکنیم. موقعی که 2 یا 3 نمونه، تحت تأثیر تنشی در حداقل تعداد دور به شکست نیانجامد، آن تنش را به عنوان حد تحمل انتخاب میکنند. اما برای مواد بدون حد تحمل، حداکثر تنشی که به ازای آن 2 یا 3 نمونه حدود 100000000 تعداد دور را بدون شکست انجام دهد، به عنوان حد تحمل انتخاب میشود. برای افزایش تعداد تناوب مجاز در یک قطعه لازم است تنش وارد بر آن را کاهش داد. میزان حداکثر تنش را قبل از شکست حد تحمل (استحکام دائمی) می نامند. هرگاه تنش وارد بر یک ماده پایینتر از حد تحمل باشد، آن ماده میتواند تحت آن تنش تعداد دور تناوب فوق العاده زیادتر را تحمل کند. برای فولادها و بعضی از مواد دیگر نسبت به حد تحمل به استحکام کششی در حدود 5/0 است. به عنوان نقطه شروع شکست مواضع زیر مورد سؤال قرار میگیرد:
نقطه شروع شکست
- عیوب ناشی از کربنگیری کنارههای قطعه، فازهای رسوبی، ناخالصیهای غیرفلزی، عیوب داخلی، کلیههای محلهای تجمع تنش، سوراخها، کنارههای تیز در محل انتقال سطح مقطعها و شیارهایی که در طراحی اجتناب ناپذیر بوده یا شیارهای ریزی که احیاناً در اثر عملیات پرداخت کاری سطحی به وجود آمدهاست.
- در تمام این گونه مواضع (نقاط ضعف) تحت تأثیر تنشهای متناوب با انجام فعل و انفعالات میکروسکوپی ابتدا یک ترک بسیار ریز سطحی ایجاد میشود که در اثر ادامه بارهای تناوبی رشد می یابد تا جایی که سطح مقطع باقیمانده دیگر نتواند بار وارده را تحمل کند و سرانجام قطعه در اثر خستگی مجبور به شکست ناگهانی میشود.
- در آزمایش خستگی نمونه باید دقیقاً صیقل و پولیش داده شده و بدون عیب سطحی باشد. تأثیر بعضی از فاکتورها را میتوان تخمین زد. بدین ترتیب که حد تحمل یک نمونه پولیش داده شده تقریباً 20 درصد بیشتر از یک نمونه پرداخت کاری شده با سنگ سمباده و حدوداً 40 درصد بیشتر از یک نمونه شیاردار از همان جنس است. تأثیر موقعیت سطح خارجی در فولاد با افزایش استحکام بیشتر میشود. برای مثال موقعی که پرداخت کاری با ماسه پاش انجام میگیرد یا یک لایه سطحی سخت تر به وسیله کربن دهی یا نیتروژن دهی یا با تغییر شکل جزیی سطحی بدست آید، حد تحمل میتواند تا حدود 25 درصد افزایش یابد. قطعات بزرگتر ماشینها با قطر بیش از 5 سانتیمتر معمولاً دارای حد تحملی حدود 20 درصد بیشتر از نمونههای آزمایشگاهی است.
- یکی دیگر ازعواملی که باعث کاهش حد تحمل میشود خوردگی است که به جز در مورد برخی از فولادهای پرآلیاژی میتواند حد تحمل را شدیداً (حدود 80 درصد) کاهش دهد. در چنین شرایطی باید قبلاً پیشگیریهایی از قبیل پوشش دادن با فلزاتی از قبیل روی یا کادمیم به عمل آورد.
خستگی زود رس
عامل دیگری که بر روی حد تحمل تأثیر میگذارد تنشهای متناوب اولیه اعم از تنشهایی با دامنه بزرگتر یا کوچکتر از حد تحمل است. بدین ترتیب که برای مثال هرگاه یک قطعه ابتدا تحت تأثیر یک تنش متناوب بزرگتر از حد تحمل قرار گیرد، حد تحمل آن به اندازه قابل توجهی کاهش می یابد ( خستگی زودرس).[3]
تمرین دهی برای بالا بردن حد تحمل
برعکس چنانچه تنش متناوب قبلی از مقداری بسیار پایینتر از حد تحمل شروع شود و به صورت گام به گام به آن افزوده شود حد تحمل را افزایش میدهد. این پدیده در عمل دارای اهمیت زیادی است و آن را تمرین دهی برای بالابردن حد تحمل می نامند.
منابع
- https://en.wikipedia.org/wiki/Fatigue_(material)
- Bathias, C. (1999). "There is no infinite fatigue life in metallic materials". Fatigue & Fracture of Engineering Materials & Structures. 22 (7): 559–565. doi:10.1046/j.1460-2695.1999.00183.x
- https://engineering.purdue.edu/LAMPL/research_peening.html Jump up ^
https://web.archive.org/web/20170107095841/http://www.prnewswire.com/news-releases/material-technologies-inc-completes-efs-inspection-of-bridge-in-new-jersey-58419432.html "Material Technologies, Inc. Completes EFS Inspection of Bridge in New Jersey". Press release regarding metal fatigue damage to the Manahawkin Bay Bridge in New Jersey
https://doi.org/10.1177/1056789506058605
Can Yıldırım, Halid; Marquis, Gary; Barsoum, Zuheir. "Fatigue assessment of High Frequency Mechanical Impact (HFMI)-improved fillet welds by local approaches". International Journal of Fatigue. 52: 57–67. doi:10.1016/j.ijfatigue.2013.02.014.
The Alexander L. Kielland accident, Report of a Norwegian public commission appointed by royal decree of March 28, 1980, presented to the Ministry of Justice and Police March, 1981 ISBN B0000ED27N
Coffin Jr., L.F. (1954). "A study of the effects of cyclic thermal stresses on a ductile metal", Trans. ASME, Vol. 76, pp. 931–950